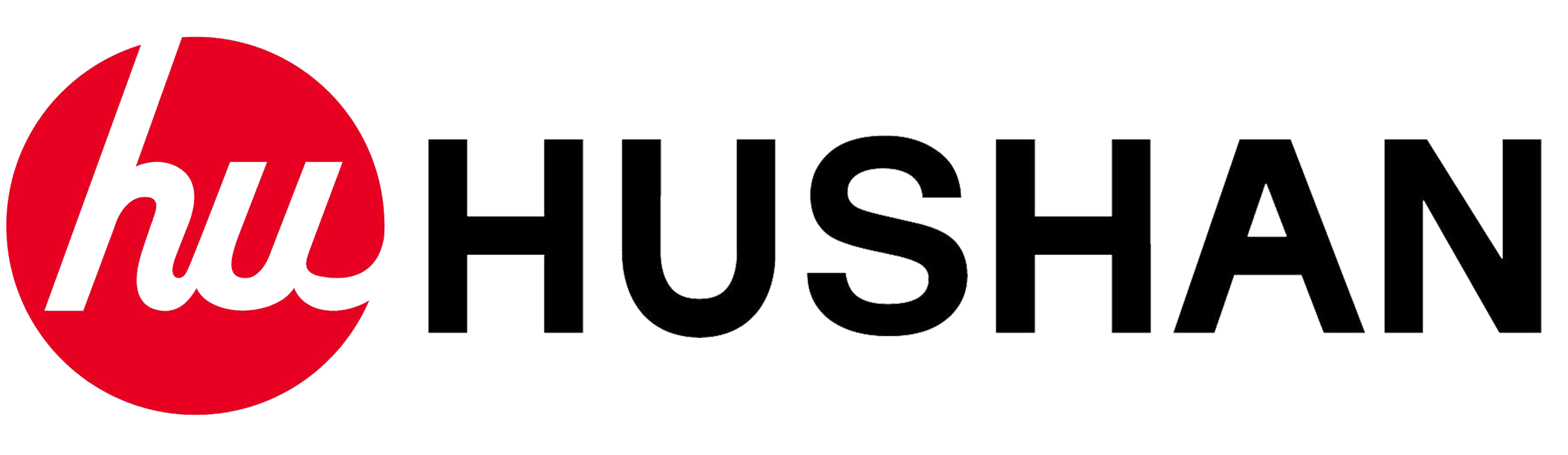
- 客戶: 虎山實業股份有限公司
- 產業: 汽車
- 解決方案: Moldex3D eDesign
- 地區: 台灣
大綱
虎山實業一直苦於無法解決縫合線問題,對於縫合線帶來的品質影響束手無策。希望藉由應用Moldex3D模流分析軟體找出縫合線分佈,用不同的設計變更組合找出消除縫合線的方法,以及驗證設計變更的可行性。
挑戰
產品末端出現明顯縫合線 (如下圖所示),而虎山這類的把手案件非常多,模具廠告訴他們不論如何修改模具都無法避免結合線出現在外觀面。希望透過模流分析驗證模具廠的想法是否正確,更希望透過解析原理,進而找出合適的設計方式,以最低修改幅度解決縫合線問題。
解決方案
利用Moldex3D eDesign方案快速建立真實三維網格模型,協助虎山實業能夠針對澆口位置及產品厚度自由進行設計變更,讓設計符合產品實際生產需求,卻無需耗費實際試模和修模費用,不但成功化解惱人的縫合線問題,更能兼顧產品品質與成本。
效益
除了調整產品厚度之外,改善產品縫合線位置的方法還可以從更改澆口位置著手,以此原則使用CAE軟體共進行了46組設計變更,從中選定最佳幾何設計進行修模。以小型產品為例,修整模具約5~10萬進行估算,一組模具需要50~100萬不等。由此結果計算,可以免去進行其他45組設計的修模或開模費用,省下的成本十分可觀。
案例分析
虎山實業欲進行修改的模型為車門內門把,此產品以單澆口進行射出成型時,機構設計出現縫合線。車門門把因使用次數頻繁,且為外觀件,產品的外觀及耐用度要求都很高;若門把出現縫合線,成型後產品的強度及外觀上都會受到影響。由於此產品已開模生產,生產時卻發現產品末端出現明顯的縫合線,因此希望能藉由模流分析,以最低成本及最低修改幅度為前提,降低模型縫合線的可見度及長度,避免縫合線問題影響產品外觀及強度。
圖一中為產品設計,圖二中為產品之厚度分布圖。由圖二中可知,產品原始肉厚設計為均一厚度,未出現厚度差。
由圖三中可知熔膠於不同充填時間下的流動波前位置,圖四中表現出原始產品設計下,出現縫合線位置和其充填時間,由此可知縫合線交會角度及出現縫合線長度。
由圖五中可知,原始設計下流動結果呈現出之縫合線長度約9.5 mm,會合角度為約90°。
圖五 原始產品設計縫合線長度及會合角度
波前接觸的角度視為縫合線出現與否的重要參考依據。根據熔膠接觸的角度開始計算縫合線的長度,由判定的結果來看,熔膠波前夾角在大於90°或135°以上,可以視為分子排列方向近乎一致,不會再有縫合線產生。
經多組澆口或產品肉厚設計變更測試後,最終決議之設計變更如下方圖中所示,以下一一進行說明。
厚度設計變更:
將孔洞處厚度加厚,平面中心位置減薄,引導波前於孔洞周圍流動較快速,使兩波前交會於邊緣位置,交會角度較大且長度較短,可得長度較短之縫合線。
厚度變化斜角設計:
利用斜切設計使厚度產生變化,目的為引導流動波前於孔洞周圍位置流動較快,外圍則可流動較緩,藉此使波前交會位置為縫合線影響較小位置,且交會長度較短。
圓柱設計變更:
將波前交會位置附近圓柱設計更改為空心柱,減少熔膠充填入之體積量,使左方之流動波前不因圓柱設計而出現流動遲緩狀態。
經設計變更後流動波前結果如下圖中所示:
圖十二 設計變更後縫合線長度及會合角度
此產品經過整體結構設變及澆口位置變更後,從模擬結果發現,藉由降低產品厚度及結構角度改變熔膠波前,進而修正結合線會合角,成為最佳設計變更方案。原始設計中的產品面縫合線長度為約9.5 mm,經由設變後縮短近50%,縮短至 4.3 mm。
此專案一共進行了46次設計變更,終於找出這類車門把手的縫合線規則,並了解形成的原因。若以傳統試誤法進行,一定無法將心中的疑惑落實成科學化的數據,只能受限於模具廠而無法將技術能力厚植在自身的技術能量中。藉由Moldex3D模流分析進行設計變更並選擇設變中的最佳幾何設計,可省去未來不著頭緒的修模和試模,大幅減少成本支出。