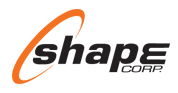
- 客戶: Shape Corp.
- 產業: 汽車供應商
- 解決方案: Moldex3D eDesign
- 國別: 印度 & 美國
Shape是一家碰撞能量管理系統以及有擁有先進的輥軋成型技術領域的領袖技術,也是北美洲地區目前最知名的汽車保險桿製造商,此外Shape 也為其他辦公家具、農業及醫療保健行業提供產品和服務。作為全球唯一保險桿產品系統式服務的供應商,可從設計、測試到生產以及其他後測試項目提供完整性的系列服務, Shape為全球不斷變化的市場提供創新、輕量、高品質及高成本效益的解決方案。
Shape 成立於 1974 年,總部設在密歇根州 Grand Haven,是擁有五家長期穩定供應鏈系統公司的私人企業,並且在美國、中國、日本、墨西哥、印度和德國設立了14家辦事處、八家生產工廠、六家製造聯盟、兩家技術中心和一家健身設施,員工超過 1,300 名。 (資料來源:shape-corp.com.cn)
擋泥板為安裝於輪胎的上端的零組件,其用途是用來保護預防車輛內部的主體在高速行駛下被石頭,
灰塵或有害物品擊中而損壞。
大綱
目前汽車行業正朝向製造更薄、更輕的零件以減少重量,而同時零件必須仍然滿足其堅固、耐久性的結構性要求。因此,閥式澆口熱澆道的技術逐漸地應用於擋泥板的生產製造中,此技術有利於控制注塑的流量、時間、縫合線的位置和模具內的壓力,進而達到輕量、省料又符合產品品質要求的目標。此案例中我們使用閥式澆口技術和不同厚度的導流設計,以幫助塑料在物件不同區域內流動能夠平衡,同時可以降低射出機高噸數的需求。為了進一步了解此注塑過程,Shape 使用Moldex3D Shell網格快速模擬多組不同的設計變更,Shape將不同厚度的導流設計加入於物件上不同的區域,希望可以藉此消弭縫合線的產生和達到塑料流動平衡狀態。透過模擬取得最佳的設計變更組的條件加入最後的產品設計,並同時與Moldex3D eDesign 3D網格技術進行模擬交互比對。Shell和3D網格的模擬結果比對中,可以發現Moldex3D Shell是可靠、又適合短時間內必須做出多組設計變更的工作流程的迅速分析方式;而Moldex3D eDesign的分析則可以提供更全面精準的分析結果,進一步在開模前驗證產品最佳設計,為產品品質嚴格把關。
挑戰
Shape在產品與模具設計過程中,遇到了不少挑戰:
- 找出最理想的閥式澆口設計,以達到流量均衡狀態
- 加入導流設計以達到流動平衡,同時把產品重量控制於理想範圍之內
- 原始設計所需要的鎖模力超過原射出機的負荷
- 節省試模次數和避免開模後模具設計修改
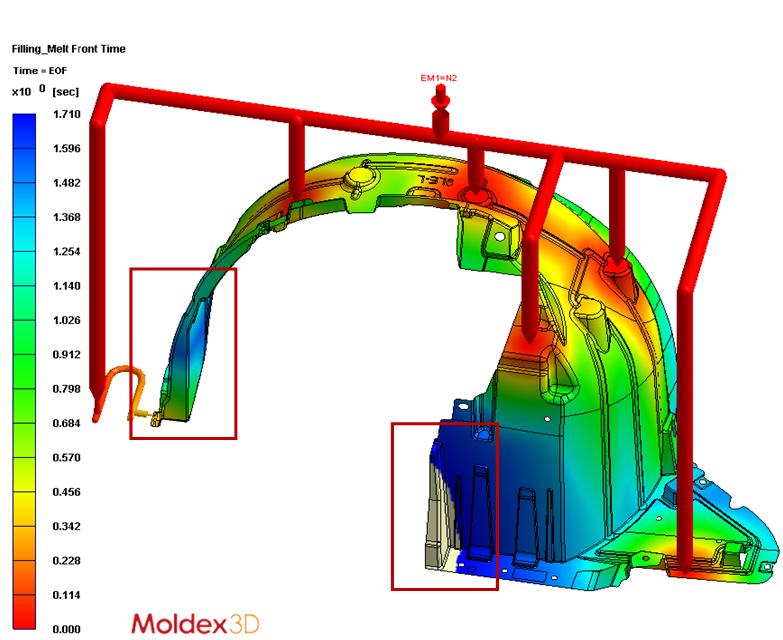
流動波前75% 流動波前100%
流動波前75% (左): 紅色圈選區域顯示包封和縫合線之產品缺陷
流動波前100% (右): 產品左邊區域比右邊還要快完成充填。右邊紅色圈選區域顯示有短射問題。
解決方案
此案例必須透過多次的設計變更,如調整澆口數量及位置、導流厚度設計與位置,加上經過多次的模擬分析,進而克服產品設計挑戰,最後達到設計最優化狀態。然而Shape必須在兩個星期的時間內完成設計變更和模流分析應證,為了達到快速又可靠的分析結果,Shape首先利用Moldex3D Shell網格技術來模擬與進行設計變更,再加上Moldex3D遠端工作管理系統,快速得到模擬結果,使得工程師能夠有效的佐證參考模擬數據並應用於下個設計變更中,因此大大地提升了其工作速度與效率。接著,在決定最後的設計變更條件後,Shape 再次利用Moldex3D eDesign真實三維的模擬技術來進一步幫助確認最終設計,而最後eDesign準確的分析結果與實際試模的結果貼近,再次證明了Moldex3D領先的模流分析技術。
案例研究
首先,為了初步了解原始設計的流動現象和所需的射出機鎖模力,Shape選擇Shell網格技術和利用全8 CPU核心運算能力,跑了一次模擬分析,並且在短時間內就得到初步分析結果。然而,初步模擬結果顯示原始的設計所需要得鎖模力明顯的超過原射出機的最大負載,Shape勢必要進行設計變更。透過改變澆口數量與位置和增加導流的設計,在不增加鎖模力的狀況下,改善流動平衡,達到最佳理想狀態。然而每個導流的設計建議都必須事先經過Shape內部工程團隊與客戶的同意才可進行變更,而且加上嚴峻的時間限制,必須在有限的時間內完成設計變更,所以Shape決定利用Moldex3D Shell 網格技術快速地進行模擬驗證,多次修改導流位置和厚度設計以確保流動平衡達到最優化,在兩個星期內進行了多達20幾次設計變更與模擬驗證。最後,透過Moldex3D的模擬分析幫助,Shape 最終得以將鎖模力降至原射出機可負載的範圍內,並且把物件左右兩邊原本相差懸殊的充填結束時間控制在只有0.2秒差之內。另外設計變更後,產品缺陷如包封等問題都能有效的控制解決,而且把後處理工作降低至最小,即可達到最理想流動平衡狀態。
利用Moldex3D Shell 網格技術快速的得到模流分析結果,爭取時間進行設計變更,如增加導流設計和改變原始塑件設計,
成功在短時間內達到最佳理想設計。
接下來,Shape工程團隊把模擬結果反饋給產品設計端,以修改最後部分產品設計。在決定最後的產品設計後,Shape 工程團隊也利用Moldex3D eDesign 3D網格進行全方面模擬分析,並將Shell 和eDesign的模擬結果與真實試模結果進行交叉比對,無論是Shell 還是3D建模分析都提供了可靠與貼近真實射出成型的分析數據。
Moldex3D模擬結果成功預測真實射出成形現象,包括流動行為、壓力、所需鎖模力的預測等等
效益
使用Moldex3D Shell和Moldex3D eDesign分析,Shape得以進行設計變更使其達到理想流動狀態、確定最佳的澆口數量與位置、和成功實現降低所需射出機噸位的改善,也因此Shape成功地避免一筆顯著的支出來進行模具改造。
項目 | 內容 |
試模支出 | Moldex3D虛擬試模幫助深度了解流動行為和所需加工條件,經過設計變更達到最佳化,因此節省約6次的試模花費。 試模花費: $1200 USD * 6 =$7,200 USD |
人力支出 | 依照過去經驗,類似的物件因為複雜度需要2位工作人員操作。經設計變更後簡化製程複雜度,只需要1人操作即可。 人力支出節省: 1 (人) * $20 (操作人員工資/小時) * 1650 hrs (所需時間) = $33,000 USD |
修模支出 | 透過Moldex3D 虛擬試模幫助改善流動不均問題,達到最優化的產品與模具設計。Shape 免於更改熱澆道的數量/位置,節省了2-3次的修模費用($10,000 USD/模穴)。 修模支出: $10,000 * 3 * 2 =$60,000 USD |
預估可節省費用 | $7200 + $33,000 + $60,000 = $100,200 USD |
此外,由於Moldex3D的強大的運算能力包括:多核心運算、遠端工作管理系統、高速計算能力,迅速有效的幫助Shape 在有限的時間內快速地取得分析結果,根據Moldex3D可靠的分析數據,成功說服Shape的客戶及時地同意其設計變更方向,而Shape也得以如期地完成模具的建造。試模的結果與Moldex3D模流分析進行比對,證實Moldex3D的分析與真正現場結果接近,可為使用者提供寶貴的參考數據。另外,此專案整個工作團隊,包括Shape的客戶,皆為了這次專案能夠在短時間內完成並產出傑出結果感到無比興奮!本案例可說是充分展示Moldex3D模擬分析如何幫助其用戶在有限的時間內完成產品設計和優化最好的例子,Moldex3D得以解決複雜和具有挑戰性的設計和製造問題,協助節省大量成本並開發適合模具得以成功量產產品。