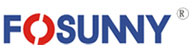
- 客戶:深圳市福昌電子技術有限公司
- 產業:電子
- 國家:中國
- 解決方案:Moldex3D eDesign
大綱
為降低生產成本與能源的消耗,CAE輔助射出成型技術在業界已逐漸被廣泛運用。福昌公司也將此技術應用在生產製造電信通訊、機殼類等產品上,以Moldex3D eDesign來進行產品的驗證及優化。透過Moldex3D eDesign的模流分析,福昌公司在實際試模和生產前,就可先行了解塑膠的流動行為及注塑過程中會產生的問題,並通過調整進膠方式、更改水路佈置與優化成型條件,不只節省了塑膠材料,更提升產品品質、縮短成型週期。
挑戰
- 翹曲變形
- 縫合線
- 應力痕
解決方案
籍由Moldex3D eDesign,在開發初期驗證產品設計(圖一)與模具設計,並比較實際試模與模擬分析的差異。隨後根據模擬結果,改變進膠方式及變更設計,再進一步運用此模組進行分析驗證。
圖一 產品設計
案例研究
此案例主要目的,是希望藉模流分析結果來評估最佳的進膠方式、水路佈置與成型參數設定,以解決手機電池蓋類產品因厚度太薄而產生的難充填、壓力過大及變形的難題。目前手機類產品常選用的三點和多點潛式澆口進膠,則使產品的壓力分佈不均勻,造成收縮不均而出現翹曲變形(圖二)。要解決此問題,就必須進行後續的加工校正,製造成本便隨之提高。這樣的設計也容易產生縫合線,使得產品的表面要經過多次噴塗才能掩蓋痕跡。然而現在客戶對產品外觀的要求越來越嚴格,噴塗方式漸不可行,且會使成品完成周期過長。
圖二 傳統三點進膠,產生壓力分佈不均情形(左圖圓圈處),以及明顯的縫合線(如右圖紅線所示)
針對這個難題,福昌公司利用Moldex3D eDesign找出合理的進膠方式,將原本三點進膠的設計改為單點進膠(圖三)。分析結果顯示,這項改良使得壓力分佈變得均勻許多,順利解決收縮不均導致的變形問題。同時縫合線也大幅改善,剩下產品結構中的孔洞所導致的輕微縫合線,只要增加成型後期的模具溫度就可輕易遮蓋。
圖三 改為單點進膠後,產品澆口處的壓力雖相對較大(如左圖圓圈所示),但其他區域的壓力分佈相對較均勻;
縫合線問題也大為改善,只剩產品結構造成的輕微縫合線(如右圖圓圈所示)
除了進膠方式的問題之外,原始產品設計還有厚薄不均而容易產生應力痕的問題。因此在使用單膠口位置的前提下,進行設計變更,在產品厚度變化處增加了過渡區域(圖四)。
圖四 原始產品(左圖)在中央區域有較薄的設計;設計變更後,在厚度變化處增加了過渡區域(如右圖紅色區塊所示)
變更設計之後,利用Moldex3D eDesign針對原始和改良後的設計分別進行模擬分析。從分析結果(圖五)可看出,原始設計在厚度變化處有明顯的剪切應力集中,進而產生應力痕。改良後的設計則沒有剪切應力特別明顯的區域,最後製造出的產品表面光滑,應力痕問題順利解決。
經模流分析之後再進行產品實際試模,赫然發現Moldex3D的模擬結果與試模結果具有高度的一致性。(圖六)
圖五 模流分析結果顯示,原始設計有產品厚薄不均問題而導致剪切應力明顯集中(如左圖),
改良後的設計則沒有應力明顯的區域(右圖)
圖六 實際試模結果顯示,原始設計的厚薄不均造成應力痕(左圖),
改良後的設計順利解決此問題(右圖),與模流分析結果有高度一致性
Moldex3D eDesign可以讓使用者自行更改進膠方式以及水路位置,也可選擇材料和設定成型參數,包括塑膠充填時間、充填壓力、螺桿的位置、冷卻水溫和成型週期等。透過模擬分析結果,可充分了解到塑膠產品在充填過程中的流動情形、充填壓力的分佈情況等,以達到理想的效果。藉由Moldex3D eDesign的幫助,福昌公司得以全面地驗證原始設計,增加新的改善方案,並了解到模擬分析與實際試模結果的差異,並一舉解決了縫合線問題、減小了產品的充填壓力、降低翹曲變形量,進而縮短產品的成型週期。
效益
分析結果顯示,經過Moldex3D eDesign的模擬之後,產品的壓力減少20%,變形量獲得了控制:X軸方向的變形量降低了50%;Y軸的變形量降低了55%;Z軸的變形量降低了30%,產品因薄件所導致的壓力過大及變形等問題已明顯改善,使產品尺寸能夠符合要求(圖七)。同時產品的縫合線問題和厚薄不均導致的應力痕問題也順利解決,縮短了成品生產週期,進而降低產品後續加工校正的成本。
圖七 改善前的翹曲情形(左圖)與改善後(右圖)比較
藉由Moldex3D eDesign的分析,福昌公司能夠在製造產品前就對各種設計方案做可行性檢驗,對產品注塑過程中會出現的缺陷也進行了合理預測並預防,以提升產品品質,並大幅降低試模成本。經實際產品試模後,也驗證了eDesign的模擬分析與試模結果的高度一致性。