- 客戶:高雄應用科技大學-塑膠精密加工實驗室
- 產業:學術研究
- 解決方案:Moldex3D eDesign /Moldex3D射出壓縮模組
- 地區:台灣
大綱
隨著科技演進,塑料加工製程應用於光學組件越來越普及,而業界對產品精度的要求也越趨嚴峻。由於車燈透鏡產品的設計有肉厚不平均的特性(圖一、圖二),因此利用傳統射出成型的製程,容易產生核心層與外表層散熱不一致以及內應力集中等問題,導致產品缺陷。為了有效克服此問題,高應大塑料精密加工實驗室團隊藉由Moldex3D射出壓縮成型模擬解決方案,探討使用射出壓縮成型製造車燈透鏡的成效。透過軟件仿真分析,該團隊了解射出壓縮製程對於塑料成型的整體影響,驗證新製程的可行性,確保產品尺寸精度。
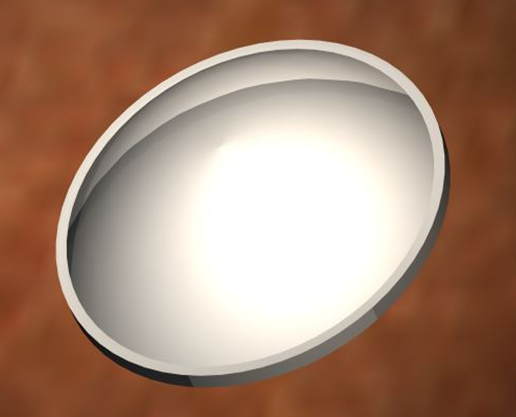
图一 汽車大燈透鏡 图二 車燈透鏡3D圖
挑戰
- 光學性質欠佳
- 翹曲問題
- 體積收縮過高(圖三)
- 殘留應力集中(圖四)
圖三 透過Moldex3D充填分析溫度等位面分佈圖,可以看到產品有嚴重的積熱和收縮問題
圖四 Moldex3D光學分析可以辨識殘留應力集中在澆口處
效益
透過Moldex3D塑料射出模擬分析與實際試模,成功驗證射出壓縮製程能有效改善車燈件質量。
- 改善體積收缩44%
- 降低翹曲量29%
- 殘留應力與光彈條紋均勻,光學性質大幅改善
案例研究
有別於一般傳統射出成型製程,射出壓縮成型具有以下優點:(1) 降低射出壓力(2) 降低殘餘應力(3) 減少分子定向(4) 均勻保壓減少不均勻收縮(5) 克服凹陷及翹曲(6) 減少成品雙折射率差(7) 緩和比容積變化(8)增進尺寸精度。
本案例希望藉由Moldex3D射出壓縮模塊來仿真分析驗證利用射出壓縮製程生產車燈透鏡的可行性,分別以產品翹曲量、體積收縮率及光學特性進行兩個製程的比較。透過仿真結果與實際射出產品結果皆證實,射出壓縮成型對於產品質量能有效的改善。
首先藉由Moldex3D分析傳統射出成型製程的翹曲量,發現由於車燈透鏡肉厚不均的設計,容易使得其核心層與外表層散熱不一致,及產生內應力集中問題,進而導致翹曲現象。改用射出壓縮製程之後,由於壓縮階段為模壁全面施壓,因此可以降低射壓,以大幅降低因壓力不均所造成的翹曲變形。圖五、圖六分別顯示利用射出壓縮製程,翹曲量可從0.7mm降低至0.5mm,成功減少29%的產品翹曲量。
圖五 傳統射出成型:最大翹曲量約為0.7mm(除去澆口與冷料井)
圖六 射出壓縮成型:最大翹曲量約為0.5mm(除去澆口與冷料井)
接下來觀察Moldex3D分析結果中的透鏡中央積熱問題。傳統射出成型製程的產品中心處體積收縮率達12.1%,相當嚴重 (圖七)。而利用射出壓縮製程後,透鏡中央溫度變得較平均,能有效改善產品收縮率高達44% (圖八)。
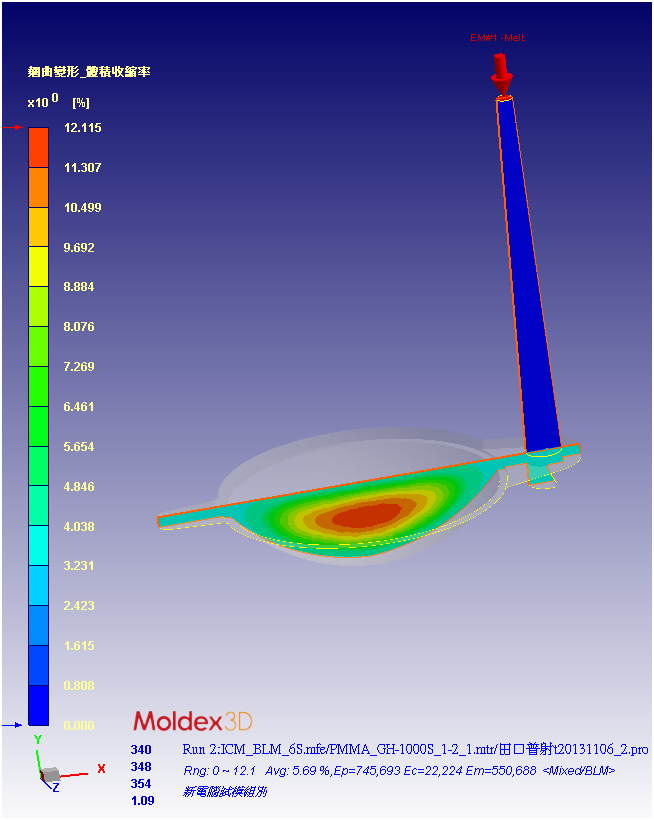
圖七 傳統射出成型:中心處體積收縮達12.1%,收縮嚴重(上)。實射產品以儀器測量測收縮凹陷量為-862.4µm (下)
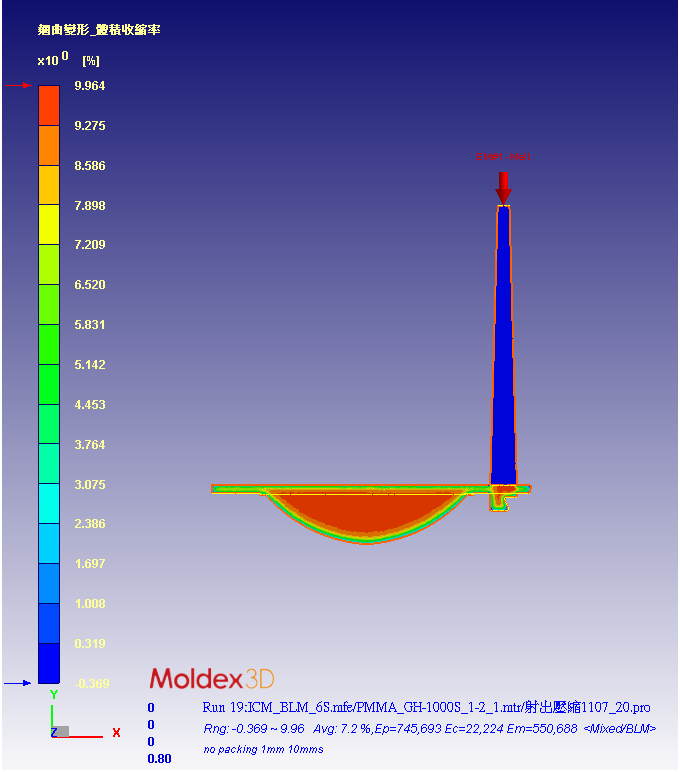
圖八 射出壓縮成型:最大體積收縮率為9.96% (上)。實射產品以儀器測量收縮凹陷量-490.5µm(下)
比較兩種製程的光彈條紋分析,傳統射出成型光彈條紋密集,光學性質差(圖九)。然而利用射出壓縮成型,光彈條紋較均勻,同時由於壓合速度越快,澆口處殘留應力較為均勻,光學性質大幅改善 (圖十)。
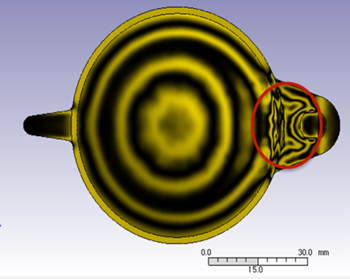
圖九 傳統射出成型:澆口處光彈條紋密集,光學性質欠佳(上)。實際射出產品光彈儀拍攝圖,也顯示光程差(下)。
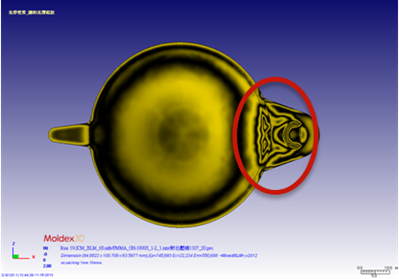
圖十 射出壓縮成型:產品本體之光彈條紋均勻(上)。實際射出產品光彈儀拍攝圖也顯示,
澆口處殘留應力較為均勻,光學性質大幅改善(下)。
結果
在此案例中,透過Moldex3D仿真分析軟件進行產品驗證及射出壓縮參數優化,協助實驗團隊加速開發及驗證射出壓縮成型製程方案之可行性。透過驗證分析,車燈透鏡產品的成型質量獲得大幅改善,達到產品尺寸穩地。實驗團隊未來希望將模擬分析的應用,擴大至優化壓縮參數研究,包含 : 壓縮力、控制位置…等,以及應用在各種肉厚產品上,探討成本效益與優化程度。