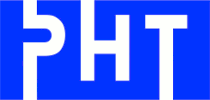
PLASTIK HT a.s. is privately owned Czech company with more than 45 years of tradition specializing in the production of technical plastic injection mouldings for the automobile and electronic industries, utilizing only the latest production technologies. Each production program is built by using four independent foundations, all bound into one tailored solution. PLASTIK HT strives to become a renowned, world – class producer of advanced plastic products and assemblies and to achieve a leading position in the production of such parts in Europe, with an impact on global markets. https://www.pehtoo.com/
Challenge
During the first trial of part sampling a problem with warpage appeared
Solution
Insert molding improved the cooling in the critical area significantly
Benefits
Final part deflection was reduced and its direction was changed to an acceptable range.
Moldex3D has been used in our company since January 2007. During that time the software proved itself to be a reliable tool for the simulation analysis to predict the cooling, filling, packing and warpage problems that may appear in a production.
Fig. 1 The warped part after first sampling
This article describes one of the problems PLASTIK HT had and was successfully solved by the aid of Moldex3D. A subcontractor made a tool and during the first trial of part sampling a problem with warpage appeared. The part was unacceptable warped in the area as visible in the picture (Fig. 1)
So there was made a simulation based on the real parameters of the tool (the whole tool was made from steel) and process conditions (Fig. 2)
Fig. 2 The tool layout and the core side of the tool
The warpage results corresponded with the real part as visible in the pictures (Fig.3a, 3b)
During the results analysis the possible reason of the unacceptable warpage was found. The cooling in the critical area was not sufficient enough and the temperature difference on the tool surface was up to 50°C (Fig.4a,4b). That difference together with quite high temperature on the part (Fig.5) may have an effect on the final warpage of the part.
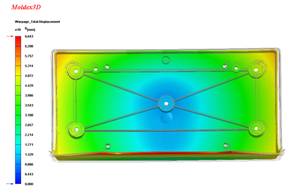
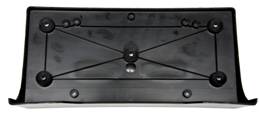
Fig. 3a Warpage results from Moldex3D Fig. 3b Real part warpage
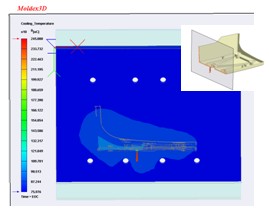
Fig. 4a Temperature difference in the mould Fig. 4b Temperature difference in the mould
Fig. 5 Temperature on the part
Based on the simulation results the tool was modified by adding an insert of a bronze to improve the cooling in the problematic area to reach the faster cooling down of the part (Fig.6).
Fig. 6 The modified tool layout and the core side of the tool with the bronze insert
The aluminum insert improved the cooling in the critical area significantly. The results showed the temperature difference was reduced to less than 15°C on the tool surface (Fig.7a,7b) and the temperature range on the part become more uniform(Fig.8).
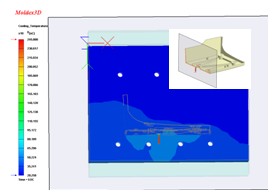
Fig. 7a Temperature difference with the bronze insert Fig. 7b Temperature difference with the bronze insert
Fig. 8 Temperature on the part from the mould with the bronze insert
The above mentioned modification improving the cooling solved the problem with the warpage. The final part deflection was reduced and its direction was changed to an acceptable range.
In the pictures below (Fig.9, 10) you can see the predicted warpage by Moldex3D and as clearly visible the results match with the deflection of the real part quite precisely.