射出成型產品開發和生產的流程中,CAE對設計工程師的確扮演著至關重要的角色,CAE分析讓設計工程師在進入實際生產前,預先排除潛在問題並進行優化設計。此外,透過CAE分析之虛擬試模幫助工程師找到合適的成型條件,以此作為後續試模的依據。當模具開發完成準備進入量產階段時,製造端無法直接於生產現場取得CAE分析後的成型條件,多仰賴經驗進行條件的調整。對於新產品或新材料,受限於經驗因素可能會加長試模過程,進而影響生產效率。由於Moldex3D CAE分析結果是依據產品、材料與機台特性下所生成,因此分析優化時所使用成型條件已高度符合實際生產情況,此種科學試模方法,相較於傳統試模,可加快試模效率與降低試模成本。如何有效共享CAE與生產端的資料,協助製造端方便取得分析結果作為試模參考資料,同時讓設計端便捷的參考試模結果作為下次產品設計與優化之參考,已成為設計與製造端間的重要議題。
近年來設計端與製造端整合的重要性越趨重要,因此在各大展場中均可看到這樣的整合結果。Moldex3D為了讓使用者可以便捷的串接製造流程,與世界級射出成型機大廠FANUC、SUMITOMO與ENGEL完成了CAE與射出機台之整合,讓模流分析結果可快速與便利的傳送到製造端,讓成型工程師參考此條件快速地展開試模流程,從而找出最合適的生產條件,減少試模時間,還能有效應對新材料或新產品的挑戰。當雙向之資料交換更加順暢時,試模數據得以輕鬆保存,重要資料存放於系統中,作為後續產品開發或產品製造的重要參考資訊。因此,當完成設計與製造端的整合,兩個階段的工作與資訊流程得以完整串連與交流,進而創造出智慧化的射出成型生產流程。
Moldex3D與FANUC ROBOSHOT射出機的整合
雙方為透過Moldex3D iSLM與FANUC ROBOSHOT LINKi2進行資料交換,其中iSLM與LINKi2均可運行於客戶端之私有雲中,確保重要資料的安全與機密性。設計工程師於地端完成Moldex3D分析,可將分析結果上傳iSLM,而在試模現場之成型工程師可透過ROBOSHOT LINKi2,直接於機台控制器上開啟與iSLM整合功能,即可在不需增加任何設備的情況下,直接於機台上查看CAE分析結果與進行雙向資料交換,相關流程如圖一所示。
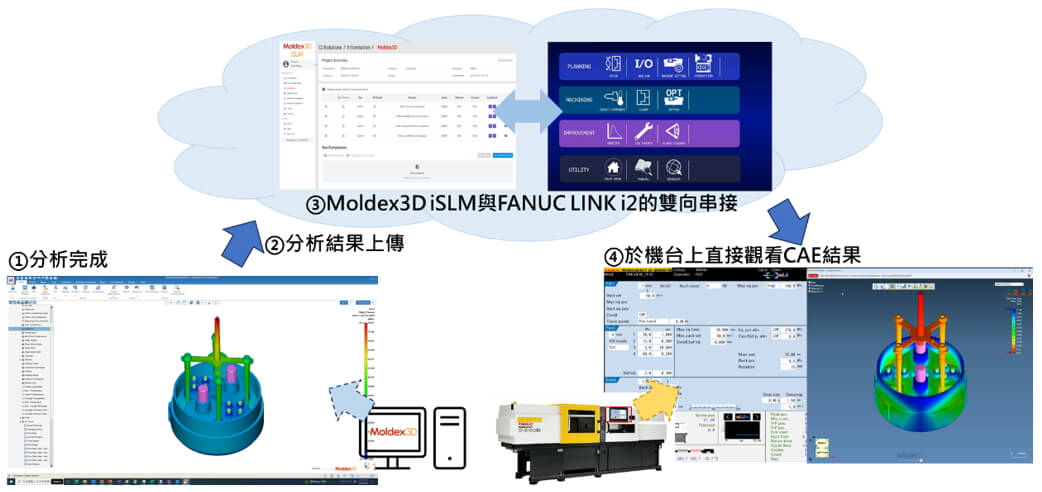
圖一 Moldex3D與FANUC ROBOSHOT射出機整合流程
成型工程師可於控制器上直接開啟iSLM,並開啟將要進行試模之分析結果,查看分析結果,例如流動波前結果、分析射出壓力曲線等,均可於控制器上直接檢視。當成型工程師要開始進行試模時,可一鍵式的快速將成型條件由CAE端傳送到製造端,作為第一次試模之成型條件,如圖二所示。成型工程師只需依據實際產品品質進行成型條件微調即可得到可量產之產品。試模完成後亦可透過一鍵式的成型條件傳送方式,讓製造端微調後之參數傳送至CAE端,除了將重要的試模結果與經驗保存於iSLM中,亦可作為後續成型工程師或設計工程師當遇到類似產品時之參考依據,加速研發與生產速度。
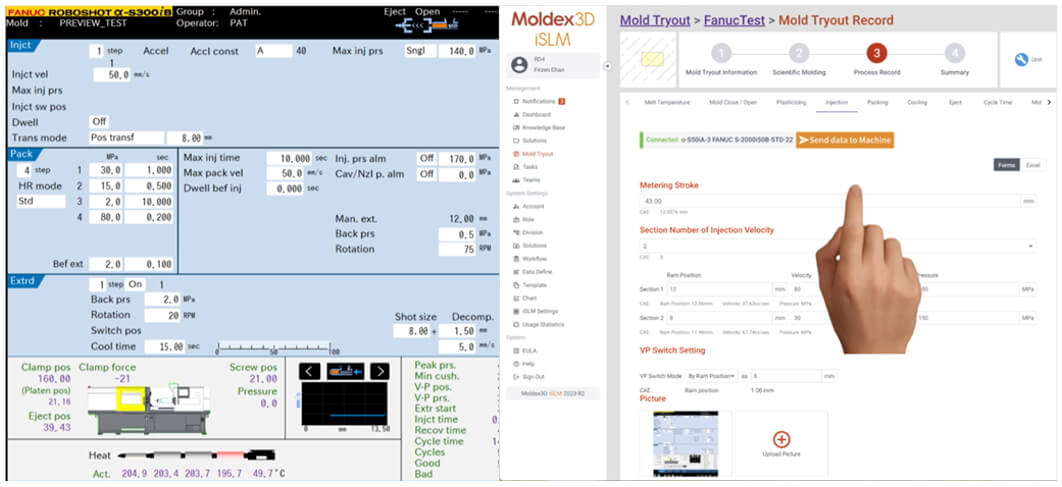
圖二 一鍵式由CAE端傳送成型條件至製造端
Moldex3D與SUMITOMO射出機的整合
雙方為透過SUMITOMO射出機可讀取之機台成型條件檔進行整合,操作流程如圖三所示。此次支援之控制器為住友NC-10控制器。成型工程師於試模前可先於將進行試模之機台控制內,完成開關模等相關設定並將機台條件檔輸出。於Moldex3D中開啟欲輸出成型條件之分析組別,進入成型精靈中開啟NC-10控制器之真實機台頁面與輸入機台檔案,使用者只需選擇欲輸出的成型條件檔與指定存放位置,成型精靈即會自動將CAE內之成型條件寫入機台檔案內,後續成型工程師只需將此檔案輸入至機台內,此時會依據此內容,將CAE條件輸入機台控制器。
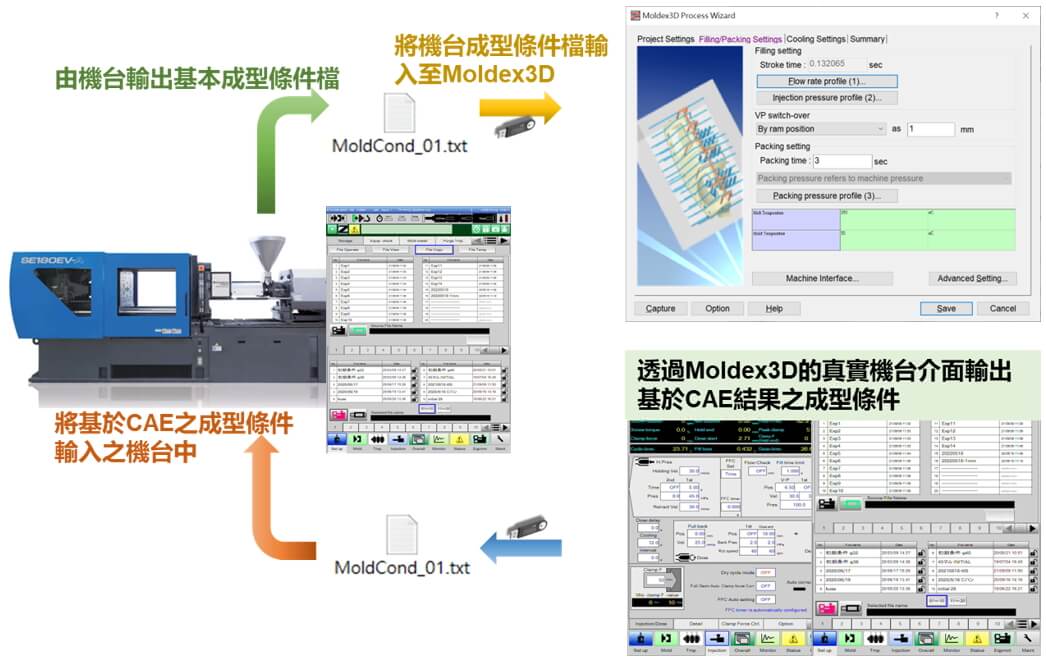
圖三 Moldex3D與SUMITOMO NC-10控制器整合之流程
Moldex3D與ENGEL射出機的整合
Moldex3D與ENGEL射出機之整合為透過ENGEL開發的生產監控和數據分析系統sim link進行。ENGEL sim link作為模流分析軟體和射出機之間交換數據的平台,結合模擬與實際生產,目前已支援Moldex3D的分析結果,操作流程如圖四所示。使用者可於本機端安裝產出Moldex3D與sim link交換檔案的程式,透過此介面,選擇分析結果專案並輸出雙方適用的交換檔案,將此檔案輸入至sim link之雲端服務中並選擇後續要生產用的機台,sim link會依據所選機台修改成型條件並生成新的交換檔,使用者再將此檔案輸入Moldex3D中,系統會自動產生一個新的分析組,並依據sim link修改之成型條件建立一個分析用之成型條件檔,重新分析後,即可獲得基於sim link修改條件後的新分析結果。重複輸入分析結果至sim link端之流程,當此結果確認可行,使用者即可將此條件透過sim link的雲端服務輸出機台可讀取之機台檔,成型工程師只需將此檔案輸入至射出機台內即可快速得展開試模工作。
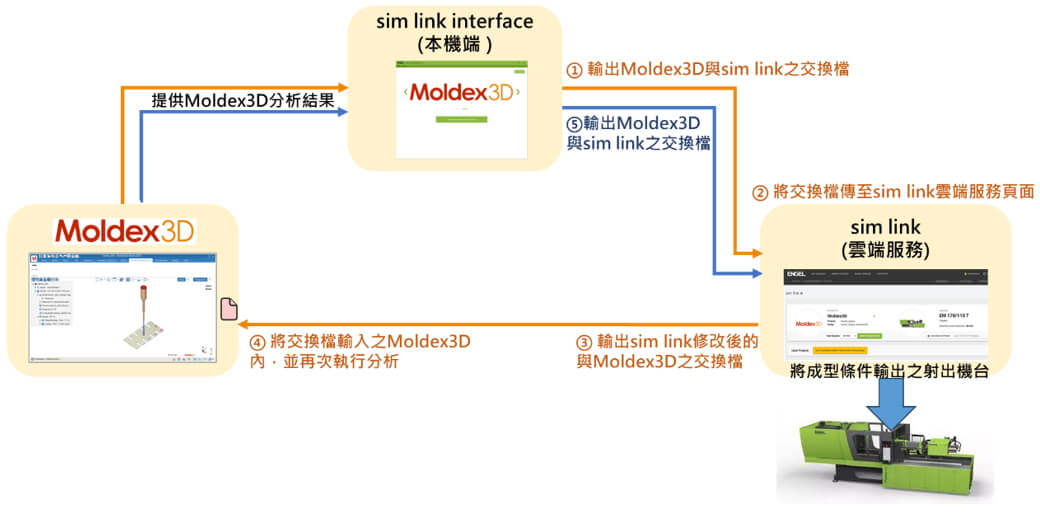
圖四 Moldex3D與ENGEL 射出機整合流程
設計與製造端整合後,模流分析結果得以輕鬆的傳送給製造端,作為成型工程師試模時的參考成型條件,進而加速試模流程。此外,透過雙方整合,關鍵的試模資料得以被儲存於系統內,可作為日後設計開發或生產的重要依據。Moldex3D透過與射出機台的整合, 與您一起面對各種產品的試模挑戰,共同創造出智慧化的射出成型未來。