現今塑膠產品的製造,多材質射出成型(MCM)製程已經廣泛地被應用於多元化的塑膠件設計與製程。MCM製程主要是利用兩種或多種材料,或使用相同的材料但不同的顏色,或是以回收材料和原料混合射出注入模具內來生產產品。利用此製程生產出的產品不僅融合了多種顏色,還可具備多種功能,比如皮層/核心層等三明治結構的組合。然而, 於現實生產中應用MCM製程,還是必須面臨許多的問題與挑戰。例如,MCM製程可能牽涉到多種嵌件、或多種不同材料,因此單一材料射出成型的設計與開發規則,常常不能直接套用於MCM。另外,由於MCM製程複雜性和多材質之物理機制,若以傳統的單一材料射出成型的經驗法則,很難推敲MCM製程與機理,因此無法有效對於關鍵成形條件進行優化或設計變更,造成品質控制上的不確定性。
![]() |
![]() |
![]() |
圖一 具有多功能性的單一產品: (a) 多顏色材質化妝品包裝瓶 (b) 模內裝配而成的玩具 (c) 耳掛式耳機。
為了進一步釐清並了解MCM製程,以期未來能進一步掌握此等製程,首先,我們可以將非常複雜多元的MCM製程歸納成為兩大類,如圖二所示。第一類為當兩種材料複合成型時,將產生明確之中間界面(distinct interface),此類常見的製程,包括嵌入成型(insert molding)、包覆成型(over molding)、和多射依序成型(sequential multiple shot molding)。第二類則為當兩種材料複合成型時,將產生不確定之中間界面(uncertain interface),此類常見的製程,包括共射成型(co-injection),雙射成型(bi-injection),針對不確定之中間界面系統,產品設計者如何能正確推測出最佳澆口位置,以及材料比例,使其成品得以獲得理想的材料分佈與產品特性,對產品設計人員將是相當大的挑戰。
圖二 多材質射出成型可分為兩大類型: (左) 有明確之中間界面(distinct interface) ;
(右) 不確定之中間界面(uncertain interface )
因此,要解決MCM製程中複雜的特性與機理,並進一步加以掌握與控制,近年來大部份團隊及成員都必須藉用CAE技術強大的模擬預測能力,以期能對潛在問題進行診斷分析並執行設計變更之事先驗證。舉例來說,小型觸控式面板,當初原始設計是針對各別組件,一件一建分開射出,再組裝而成。此方式產生組裝後產品的翹曲問題雖少,但零組件間界面結合的強度可能受到影響,而且後段再組裝也會是產品品質掌控之盲點。為此,利用MCM製程一體成形,透過包覆射出(Overmolding)成型(圖三a所示),可以改善並提高物件界面結合的強度與後組裝問題,但是製程中,由於兩種不同的材料界面互相接觸時,在後續冷卻階段將會產生區域積熱現象 (圖三b),導致產生嚴重的翹曲問題。由此可知,單件射出成型的產品設計與加工製程,不能直接套用在MCM產品製程中;而MCM製程所可能產生的翹曲問題,必須透過產品設計變更和不同的加工條件來解決。
a.
b. 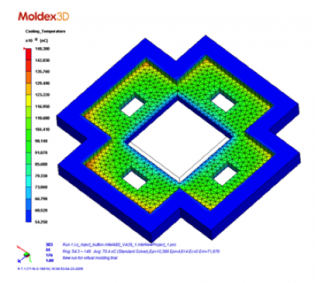
圖三 小觸控式面板產品使用多材質射出成型製程: (a) 透過包覆射出製程(overmolding),產品發生嚴重翹曲問題
(b) 翹曲問題是由兩種不同的材料界面互相接觸時,所產生區域積熱的現象所造成。
另一方面,共射成型(co-injection)製程中大多數皮層/核心層的結合可創造出許多新穎之產品,比如:產品可能為觸感柔軟的皮層/堅硬之核心層,或是純料之皮層/回收料之核心層,或是純料之皮層/含纖維強化之核心層等等的組合。若從實用面而言,共射成型製程普遍應用於汽車件、大眾消費產品、和需要加強強度結構的產品製造上。進一步從開發內涵而言,此等製程必須面臨主要的挑戰是如何控制模具內的材料分佈為理想狀態。以耳掛式耳機產品為例(如圖四所示),耳機掛鉤設計必須連接手機和麥克風功能,與人體皮膚(耳朵)接觸區域,該皮層材料必須具有良好柔軟觸感,但內在架構組成又必須具有足夠的強度,避免產品變形。
a.
b.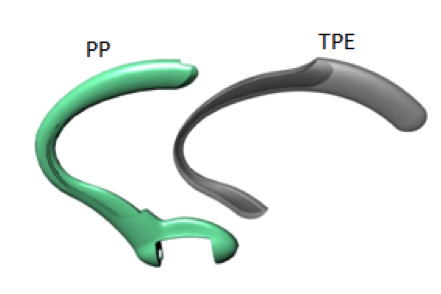
圖四 耳掛式耳機: (a)幾何設計 (b) 利用雙射/共射製程,以PP材質為核心料和TPE材質為皮層料。
當此耳掛式耳機製作採用共射技術,以PP材質為核心料,以TPE材質當皮層料。理想上,應用共射成型製程可簡化零件組裝手續的嶄新應用技術,並提供物料之間的接合界面具有更好的強度。然而,實際執行此類共射製程時,將面臨許多挑戰,例如:皮層料/核心層料之間的到底比例為何? 射出之相關條件要如何給定? 此時可事先透過CAE進行預測。 如圖五所示,根據CAE模擬預測,使用50% 皮層料比例會導致核心層穿透皮層,造成產品品質瑕疵問題。再進一步執行皮層/核心層比例調適,可能70% 皮層料比例是較佳的選擇。但是以此比例當基準,進一步預測產品變形問題時,我們發現產品具有嚴重翹曲問題,導致產品功能性不彰。
圖五 利用共射製程開發製造耳掛式耳機: 50%皮層料比例,會導致較堅硬核心層料穿透皮層料,造成產品品質瑕疵問題。
接著,我們再利用CAE執行虛擬之設計變更,執行一系列之修改模具澆口位置設計驗證,如圖六所示;我們發現一些有趣且非常實務之解決方案,例如:應用圖六(a) 所提之澆口方案,當採用40%之皮層料比例時,會導致核心層穿透皮層,原先思考這將會是造成產品品質瑕疵之嚴重問題;然而,應用CAE軟體預測事先得知,使用40 %皮層料生產此物件,反而是最佳比例,因為較堅硬之核心料,在0.07秒時會穿透皮層,穿透現象發生後,該耳掛鉤部結構件轉換為僅使用較硬的PP材料,剛好提供更好的強度以符合產品強度要求。上述利用CAE技術事先預測,順利解決產品製程與品質問題。
圖六 利用CAE模流軟體:幫助進行模具澆口位置優化驗證。
圖七 (a) CAE軟體成功幫助預測出使用40 %皮層料為生產此物件的最佳比例,此時較堅硬的核心層料穿透皮層料之現象會發生在0.07秒; (b) 穿透現象發生後,該耳掛鉤部結構件轉換為僅使用較硬的PP材料,來提供更好的強度以符合產品強度要求。
結論
多材質射出成型(MCM)在現今的塑膠產業中應用相當廣泛。然而,由於MCM製程複雜性和多材料物理機制,以傳統的單一射出成型的經驗法則來推敲MCM製程,將遭遇許多困難,無法有效提供關鍵成形條件進行優化或設計變更,造成產品品質瑕疵問題。然而透過CAE模擬分析技術,不論是包覆射出成型(Overmolding)或是共射成型(co-injection molding),都可提供有效的產品設計驗證、澆口位置優化,最大可行的核心層料比例預測(包括預測是否會發生核心層料穿透皮層料的現象),並考慮材料之間的相互作用影響,成功預測產品收縮和翹曲率來改善的產品品質的利器。
參考文獻
1. US patent #3,051,994.
2. Multi-material Technology, Battenfeld.
3. Web source https://www.engelmachinery.com
4. Chao-Tsai Huang et al, SPE ANTEC, 1888-1892 (2006).
5. P.J. Garner and D.F. Oxley, British Patent 1,156,217 (1971).
6. V. Goodship and J.C. Love, Multi-Material Injection Molding (2002).
7. R. Seldén, Polymer Engineering & Science, 40, 1165 (2000).
8. F. Ilinca, J.F. Hetu, and A. Derdouri, International Journal for Numerical Methods in Fluids, 50, 1445 (2006).