iMFLUX採用固定射出壓力(低壓)的模式,於充填過程採用一致的射出壓力,通過塑膠壓力控制成型過程,使得熔膠送至模腔時,不會失速或滯流,而波前在恒定壓力情況下連續前進,可自動調整速度,因此具有流動波前較一致的優點。由於使用較低的射出壓力,因此射出過程中的壓力峰值會低於傳統速度控制模式下的射出壓力峰值,如圖一所示。由於射出壓力較低,因此也減少由壓力所造成的產品品質問題,控制壓力可以讓射出過程提早進入保壓階段,減少冷卻時間,也降低整個射出過程的成型週期。為了有效控制iMFLUX模穴內的壓力,可藉由安裝模內壓力感測器與設定壓力控制係數PFA (Process Factor A)的配合下,透過PFA控制熔膠壓力,實現射出製程精確的控制。
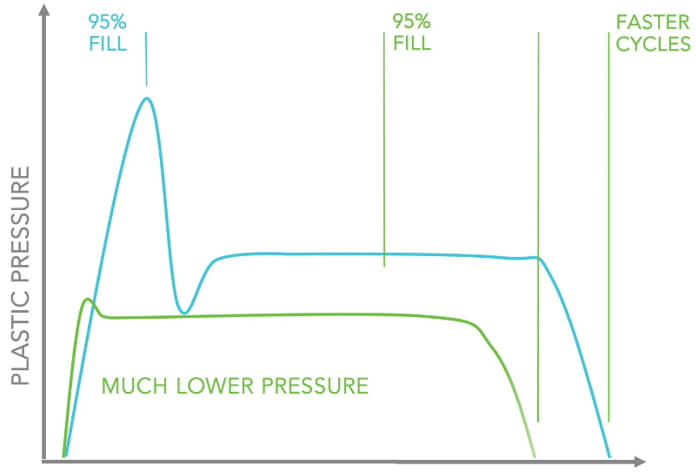
圖一 傳統射出成型製程(━━━)與iMFLUX製程(━━━)的比較
(Reference: https://www.imflux.com/)
對使用者而言,當使用iMFLUX製程時,如何選擇最佳的射出壓力與決定適當的模具感測器位置用於PFA控制參數是至關重要的。以往只能透過試誤法尋找可行的數值,現在透過Moldex3D即可進行iMFLUX製程模擬功能,如圖二所示。讓使用者在跨入此製程前可先進行效益評估,導入後也能依據模擬結果找出最佳成型壓力,避免過高的無效射壓。透過整合後之功能,Moldex3D可預測熔膠行為,找尋進行PFA控制參數之最佳模內sensor位置,達到最合適壓力調整。
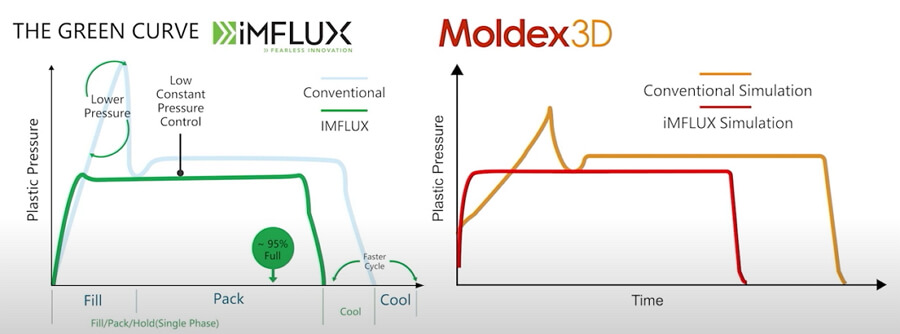
圖二 Moldex3D實現iMFLUX製程模擬
以一個盒裝產品為例,使用者可於Moldex3D中使用Create Run(s) Wizard中選擇最大保壓壓力後快速完成不同壓力之多分析組別設定,如圖三所示。
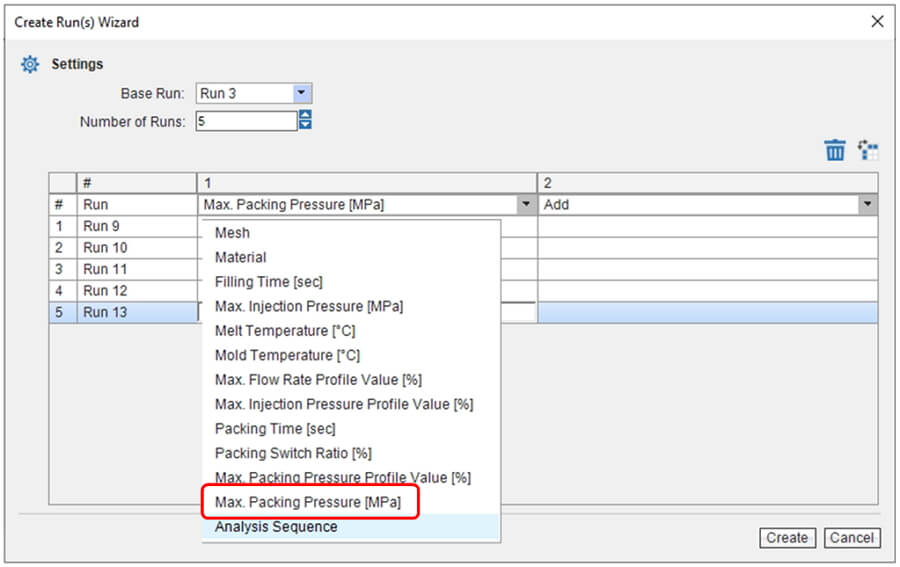
圖三 多分析組別設定
由分析結果可以看出,當壓力為25MPa時可充飽產品,如圖四所示。因此使用者無需設定超過25MPa之設定壓力做為射出壓力。Moldex3D可以在試模前了解可行之設定壓力條件,減少因為使用試誤法導致材料與能源浪費。
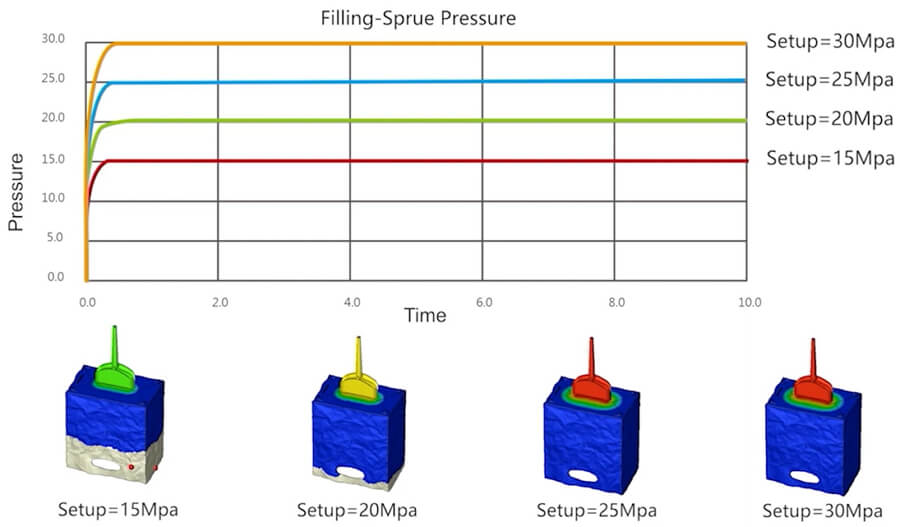
圖四 不同壓力下之產品充填結果
在設定PFA控制參數的位置選擇中,CAE的一個優點為可設置多個虛擬感測節點,進行多個感測器在產品中的設置模擬,透過CAE選擇適當的PFA控制參數運行位置,進而分析,如圖五所示。分析完成後使用Moldex3D Summary table觀察不同感測節點下的分析結果,藉此找到適當之感測結果。以此範例而言,由熔膠通過感測節點#1或測節點#2後開始進行PFA控制,如圖六所示,於此位置,產品可以得到較佳的收縮和翹曲結果與較低的鎖模力,因此可做為後續感測器安裝位置的參考。
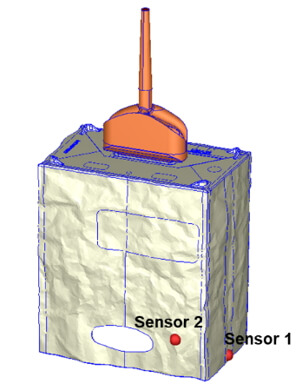
圖五 設置多個虛擬感測節點
圖六 不同感測節點之分析結果
透過於Moldex3D中的PFA設定,可於分析結果中呈現不同PFA設定下的熔膠壓力變化,圖七中分別呈現當PFA等於0.5與0.1下的壓力變化,藉此用來評估在實際生產前之適當PFA係數設定值。
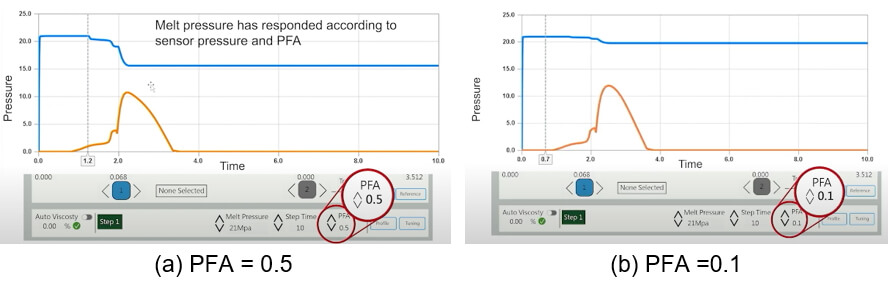
圖七 不同PFA係數下之壓力變化
iMFLUX可以有效地降低因試誤法而產生的成本浪費,並且透過分析結果縮短試模次數,進而加快產品量產時間。以往當使用者採用iMFLUX製程進行產品生產時,需透過試誤的方式尋找適當之射出壓力,若要用PFA控制時,如何在生產前選擇合適感測器位置,對使用者而言一直是頭疼的挑戰。現在使用者可透過Moldex3D中iMFLUX的模擬功能,評估其優勢,並考量是否導入此製程。當導入此製程後,Moldex3D的模擬能力可幫助使用者找到最佳成型壓力、模內壓力感測器的位置與分析不同PFA控制的效果。