By Jay Vang
Copyright MoldMaking Technology 2019. Reprinted with permission from Gardner Business Media.
直到現在,仍有許多人對異型水路抱持懷疑的態度,然而很大的原因在於沒有完整的分析工具。雖然市面上的軟體已提供很多優化工具和模組,是非常好的驗證技術;但其效果仍取決於使用者所輸入的東西,這也就是所謂「垃圾進、垃圾出(Garbage in, garbage out.)」的概念。若兩名不同的分析者在進行模流分析時,輸入不同的參數,可能會得到完全不同的結果。對於異型水路分析來說尤其如此,若輸入了錯誤的假設,或遺失重要的參數,例如須達到所需的流率以確保產生紊流等,就會導致錯誤的結果。
模擬與分析
異型水路可協助將成型週期縮到最短,並達到產品所需的尺寸。然而此結果須在設計者能維持異型水路所需的流率之前提下才可達成。對於複雜的設計,若只進行散熱模擬(僅將水路系統定義為散熱源),是無法窺探模內行為的全貌的。圖一可觀察到一計算流體力學(CFD)分析結果,呈現流率約2.0 gpm時的雷諾數。
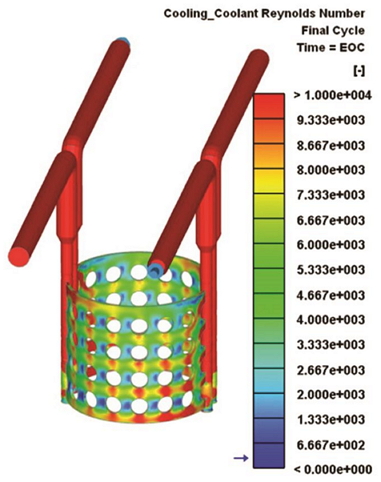
圖一 計算流體力學(CFD)分析結果,呈現流率約2.0 gpm時的雷諾數
由圖一可看到,部分區域的雷諾數高於4200,顯示有紊流現象;但其他雷諾數低於4200的區域,則不一定會產生紊流。這種情況會造成整個冷卻水路的冷卻效率不一。流速與雷諾數有直接相關,因此設計者若能找出低流動或無流動的區域,就可藉此優化水路設計。模擬也可呈現流速結果找出低/無流動的潛在的遲滯區域。須記得流體都會順著阻力最小的路徑流動,因此冷卻液會直接從進水口流往出水口,而不會循隨機路徑或往周圍孔洞四處流動。
設計者可利用這些資訊來優化水路設計,並把低流動和無流動區域盡可能縮小(如圖一孔洞間的深藍色區域)。例如可以嘗試擴大間距迫使水流通過雷諾數較低的低/無流動區域,儘管冷卻液還是會從阻力最小的路徑流動。如此降低孔洞的影響之後,可以縮減低流動和無流動區域,在一定流率下最大化紊流現象。
現在的問題是:「這樣的分析和散射分析差異有多大?」其實從冷卻計算的立場來說並不大,且要視輸入的流率而定。然而散熱分析和CFD分析的結果將決定改變的效率和幅度。
為了貼合產品幾何(如圖二、圖三),異型水路包含很多尺寸小、長度長的管線。尺寸小或厚度薄、且長度長的冷卻水路設計,需要較大的壓力,管線內才能達到足夠的流率。所以若要了解異型水路,只進行一般的散熱分析是不足的。
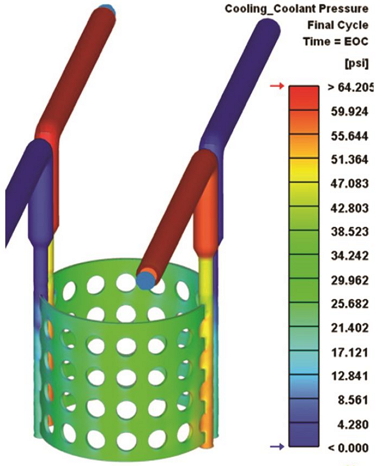
圖二 同一個模型的冷卻液壓力結果,流率也一樣是2.0 gpm
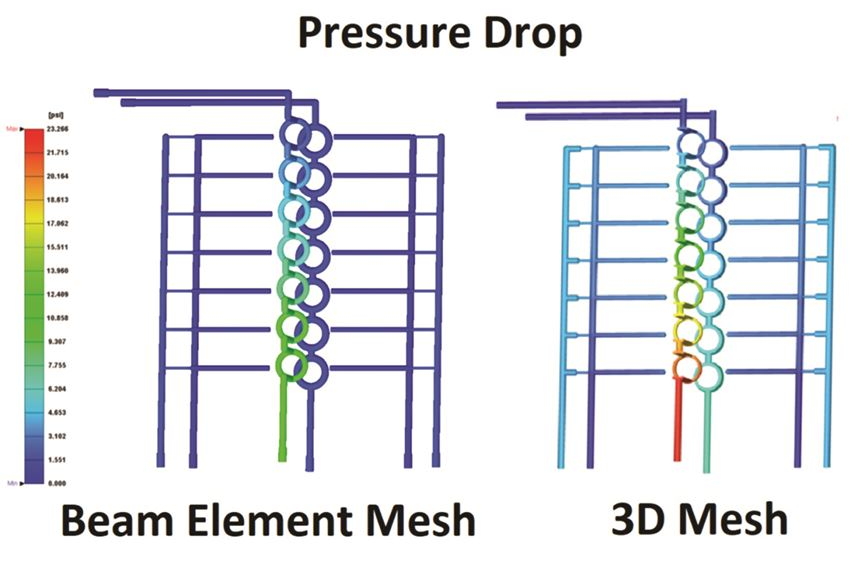
圖三 利用線架構和3D網格的壓降結果模擬比較圖,顯示推動流率所需要壓力頭,冷卻液才能通過整個管線
壓力需求
若雷諾數和流速是取決於流率,那麼一個實際的問題是:找出要達到特定流率所需的壓力,才會知道是否能達到所需的流率。圖二顯示模型的冷卻液壓力結果,流率也一樣是2.0 gpm。
流體會往阻力最小的路徑流動,為了產生紊流以確保對產品有良好的熱傳導,設計者必須了解其設計所需的壓力和最小流率。圖一即顯示流體在大部分區域的雷諾數介於4,000和10,000+之間,就有可能產生紊流(Re # > 4200)。然而要達到這個數字,就需要較高的壓力,來讓流率2.0 gpm的冷卻液流過整個管線。
目前市面上的調溫器可以產生約100 PSI的壓力,但要達到65 PSI可能也不大容易,原因是流體會流向管線中阻力較小的區域,例如熱流板、模仁和模穴板等。若流率降至低於2.0 gpm,雷諾數也會降低僅能造成層流通過線路,對於冷卻的效益是非常低的。此外,設計者若僅僅提高流至熱流板的流率,並不會使管線內的流體產生線性分布。
如果設計者沒有將異型水路和所使用的調溫器作連結,又或是並沒有使用限流器來將水推動至特定管線中,則模擬結果就會與實際情形有差距。若設計者無法達到維持整個異型水路中紊流的所需流率,還不如改用傳統式鑽孔水路,以達到同等或較佳的結果。
關於網格
透過精確的CFD分析,設計者可獲得準確且可靠的異型水路模擬結果;然而並非所有的CFD都能達到一樣的效果。接下來要解說的是模流分析軟體中,針對水路分析的兩種主要網格方法:線架構和3D架構。
線架構可呈現雷諾數、整個模具溫度的升降,以及流動分布,但在預測壓降時,準確度就不如3D架構。此外線架構對於捕捉真實的幾何也有困難,僅能利用相對體積來建模。不過線架構也有優點,即模擬速度比3D網格還要快。
圖三為比較線架構和3D網格模擬的壓降結果,顯示推動通過整個水路的指定流率所需的頭壓。雖然每條線路的壓力需求比相似,線架構中顯示在複雜線路所需的壓力少了25%至50%,而複雜的水路設計是提高壓力的潛在因素。若單只有壓降結果,會使得調溫器需求錯誤進而設計出不佳的異型水路,導致流體在流經水路時會受到限制而流量不足。
驗證步驟
為了證明3D網格能比線架構捕捉到更精確的壓降預測結果,來自 MGS Mfg. Group 的Kevin Klotz進行了壓力預測的實驗驗證(如圖四)。
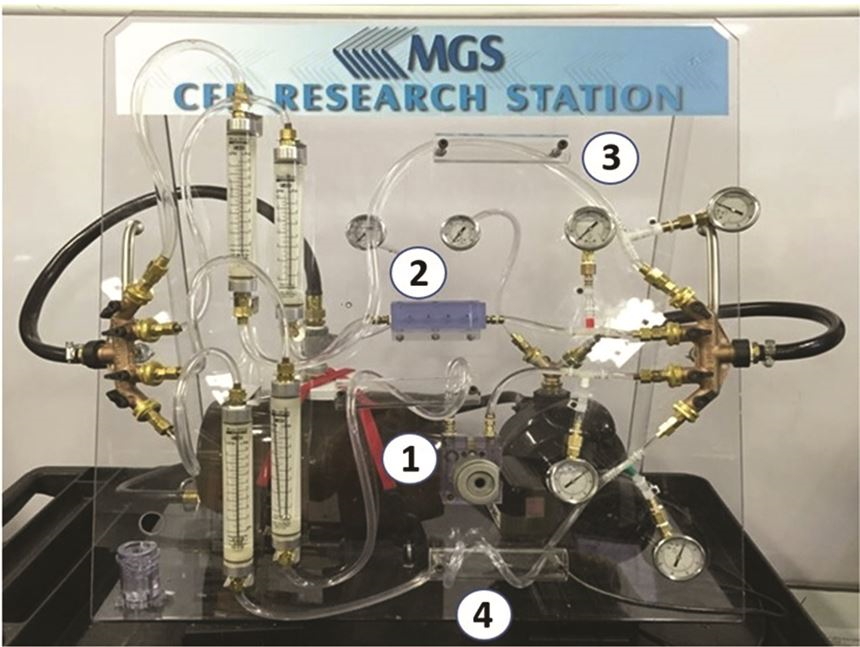
圖四 MGS Mfg. Group以實驗驗證壓力現象:(1) DMLS異型水路嵌件,(2) 3D列印的噴泉式水路,(3-4) 不同長度和尺寸的透明管及連結水幫浦和水缸的壓力表、流量計。
Klotz使用DMSL異型水路嵌件、3D列印的噴泉式水路、不同長度和尺寸的透明管及連結水幫浦和水缸的壓力表和流量計來進行實驗。此儀器是由CREO建模,其結果將被記錄下來與模擬結果比較。同樣的模型也提供給 Hoerbiger Corporation of America 的Jeet Sengupta博士,以利透過ANSYS CFX來進行CFD分析,以及用Moldex3D的3D邊界層網格(BLM)來做分析。
兩種軟體工具都以每條管線記錄的流率值,結合6.5 gpm的流率值輸入幫浦,來記錄進水口、出水口和壓力表位置的壓力。圖五顯示CFD分析和3D BLM建構模型的結果。透過3D BLM模型,設計者在進行模擬時,設定以直線接到進水口與出水口,而非彎曲管線,原因是模擬軟體中須將流體的進出水口與模面垂直。
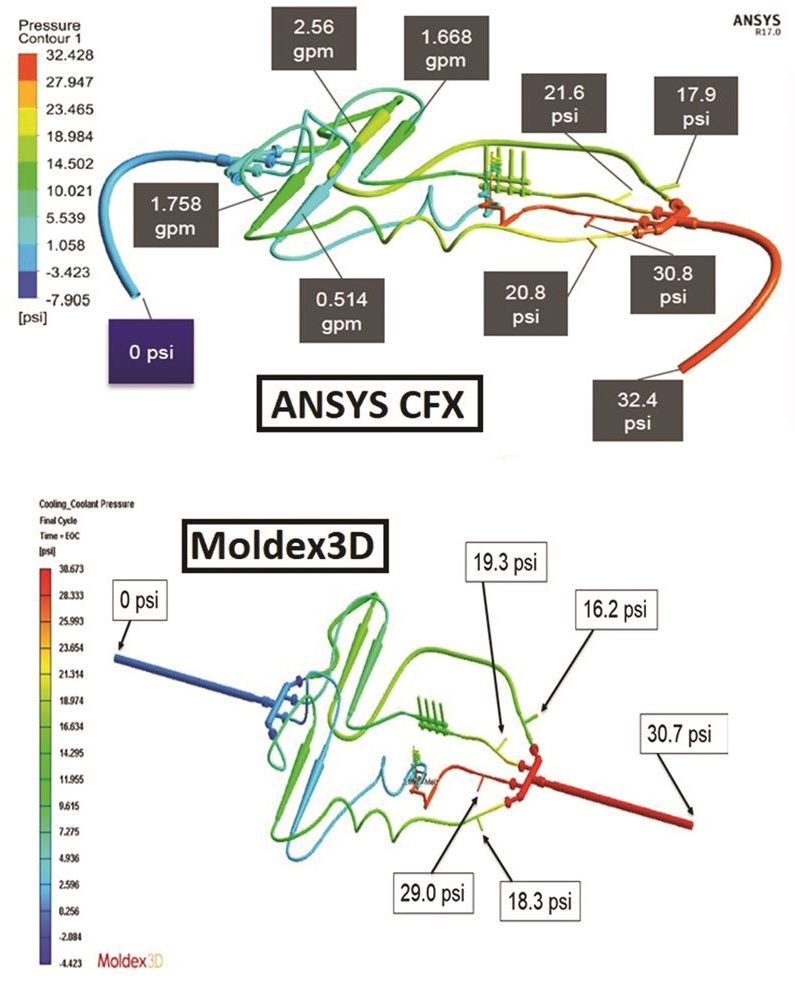
圖五 CFD分析結果及3D BLM模型。透過3D BLM模型,設計者在進行模擬時,設定以直線接到進/出水口,而非彎曲管線,原因是模擬軟體須將流體來源的進出水口與模面垂直。
兩種軟體的壓力分析結果,都與實體儀器所記錄的量值非常相近。表一為CFD分析和實際測量結果比較。其中CFD分析和BLM網格分析,與實際結果之間的最大差異分別約為5.0 psi和2.5 psi。若考量壓力表讀數和流量計所測量的流率的限度,兩種結果都在可接受的準確度範圍內。
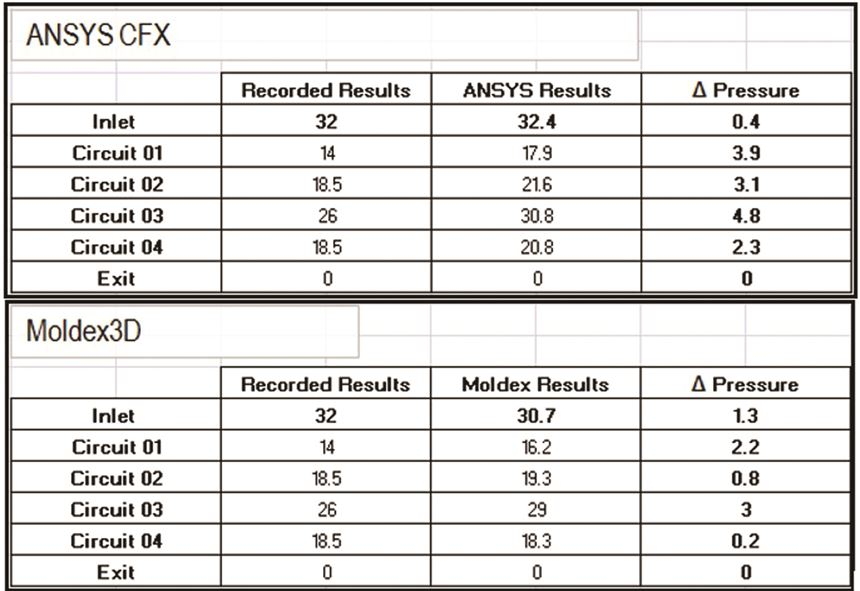
表一 壓力的實際測量值與模擬結果比較
我們學到了什麼?
倘若設計得當,異型水路的確能夠發揮預期的效益。要達到此目標,我們需要全面的CFD模擬來協助觀察流動特性。舉例來說,3D列印的嵌件若分支為兩個以上的管線,決定適合的分支,對於異型水路設計的效益將會有很大的影響。
若設計者只進行散熱模擬,將無法準確預測異型水路等複雜水路設計中所需的壓力,以達到能產生紊流的流率。然而透過3D網格架構,設計者就能精確捕捉到流體的流動特性,如動量變化等,以獲得精確的壓力分析。
![]() |
Jay Vang
|