客戶簡介
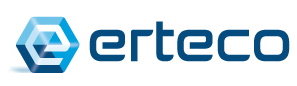
- 客戶:Erteco Rubber & Plastics AB
- 國家:瑞典
- 產業:塑膠材料
- 解決方案: Moldex3D Advanced 解決方案;流動分析模組 Flow、保壓分析模組 Pack、冷卻分析模組 Cool 、翹曲分析模組 Warp、纖維配向模組 Fiber、FEA介面功能模組、多材質射出成型 MCM
大綱
本案例中,Erteco必須找出並解決船隻螺旋槳內部的玻纖塑膠輪轂組件碎裂原因。螺槳轂在船隻負重過重的情況下,螺旋槳葉片旋轉時就容易發生碎裂問題,影響產品的整體品質和性能。
挑戰
- 縫合線造成結構脆弱,產品易發生碎裂;若以金屬軸環加強脆弱區域,成本相當高
解決方案
透過Moldex3D判別發生組件斷裂的原因,並透過模擬分析驗證新的可行方案
效益
- 優化製程條件
- 採用ETT (Ems Tape Technology )增強碳纖維膠帶,發現可與高分子聚合物完美結合
- 解決輪轂最薄處嚴重的縫合線問題和破裂問題
- 以ETT加強輪轂結構後,成功省下可觀的成本
案例研究
本專案目標為尋找另一更具成本效益的方式,來解決螺旋槳葉片和輪轂連接處在負重過重時容易碎裂的問題(圖一)。製造商Propulse原本是以人工方式將塑件放入機器中,再以金屬軸環固定以加強結構(圖二)。
圖一 Propulse的螺旋槳模型分解圖,圖中圓圈處為本案例研究的部件。(Propulse AB, 2015)
圖二 本案例原本以金屬軸環來加強結構
進行第一次的模擬分析,從流動特徵中發現會產生嚴重的縫合線,且位置與螺旋槳葉片旋轉時為輪轂帶來急劇加速度而產生巨大負重的區域相符合。該區域又是物件最薄處,因此縫合線的產生會嚴重削弱產品強度。
為改善此問題,Erteco決定改採聚醯胺纖維及碳纖維的合成膠帶 Ems Tape Technology (ETT)來取代原本的方式,並以Moldex3D驗證此新技術。模擬過程中透過感應節點來監測射出成型過程中的溫度和壓力行為。進行第一次射出測試後,發現膠帶與高分子聚合物無法完美結合。因此Erteco進行兩種不同製程條件的模擬,包括原始設定(圖三)以及提高模溫和料溫的設定(圖四)。
圖三 採用EET的模擬案例(原始設定)
圖四 調高模溫和料溫後的EET的模擬案例
Moldex3D的分析結果指出,提高模溫和保壓壓力,可協助有效預防產品收縮,而避免膠帶從母體滑落。原因是高模溫和保壓壓力會稍微拉長產品脆弱處在保壓階段波前溫度高於熔膠溫度的時間,使膠帶和高分子聚合物完美結合。
結果
Moldex3D幫助Erteco的工程師檢視塑件品質問題,並在更短的時間內針對問題進行快速的修正,達到成本效益。後續Erteco也可藉Moldex3D做進一步的分析,優化新的製程條件並改善生產品質。