- 客戶:台灣科技大學
- 地區:台灣
- 產業:教育
- 解決方案: Moldex3D Advanced /射出壓縮成型模組 / 光學分析模組 / 黏彈性分析模組
大綱
精密光學元件的射出成型技術發展至今已相當成熟,然而隨著成品精度的要求越來越高,包括殘留應力分布、翹曲及凹痕等問題都必須嚴格控制,因此成型技術的改良勢在必行。台科大精密製造實驗室期望開發模內微壓縮成型(In-Mold Micro Compression, IMMC)製程,以改善射出成型所產生的缺陷。在開發之前,先藉由Moldex3D的射出壓縮成型模組進行分析,判斷產品是否確實達到優化,以評估開發新製程的可行性。分析結果發現模內微壓縮成型在產品凹痕、體積收縮和集光效果等方面都有顯著改善;經實際試模和量測之後,同時也驗證Moldex3D分析的高準確度。
挑戰
- 壓力分佈不均
- 體積收縮率過高
- 翹曲變形問題
解決方案
藉由Moldex3D射出壓縮成型模組進行傳統射出製程和IMMC製程的分析和比較,以決定是否應用新的製程。
效益
- 壓力分佈均勻度大幅改善
- 產品光照度提升7.35%
- 體積收縮率由6.62%降低至4.25%
案例研究
圖一 本案例的複合式稜鏡為塑膠製的集光元件
複合式稜鏡是自然導光系統中的集光元件,用於室外或建築物屋頂收集陽光(圖一)。為了提升產品的導光效率,澆口位置必須避開導光處,設計於產品薄端,卻因此不利壓力傳遞和塑料流動。此外,為了提升導光效果,產品中有兩處狹縫設計(圖二),造成局部模溫較低。塑料流經模溫較低處時容易凝固而難以流動,導致壓力傳遞不易,體積收縮率也較高,使成品後端產生明顯凹痕,影響集光、傳光與出光的效果。為解決這些難題,台科大精密製造實驗室運用Moldex3D模流分析軟體,評估開發模內階段式射壓成型製程,是否能夠獲得較優化的產品。
圖二 產品有兩處狹縫設計,會導致流動不平衡情形
首先藉由Moldex3D來進行射出成型製程的分析。在凹痕指標的分析中,圖三(左圖)顯示產品厚段處的凹痕指標大,原因是內部塑料溫度高,使得表面向內收縮而導致凹痕。圖三(右圖)則顯示產品第三齒處有較大的凹痕位移,表示產品末端體積收縮率大,以致平面度不佳,降低集光效果。
圖三 進行射出成型製程分析,保壓結果中的凹痕指標(左)及凹痕位移(右)情形
接下來利用Moldex3D進行模內階段式射壓成型的分析。分析結果發現,IMMC製程的體積收縮率,比傳統製程少了 18.9%(圖四)。在翹曲變形的部分,從翹曲分析結果中的Z方向位移,也可看出IMMC製程比射出成型優化了71%(圖五)。
(a)
(b)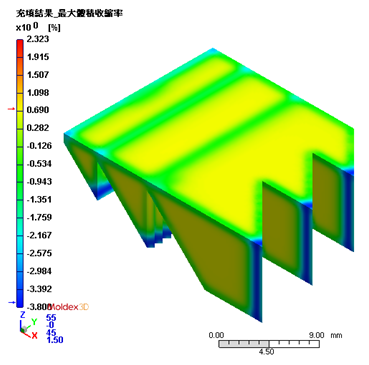
圖四 保壓結果的體積收縮率比較:圖(a)為傳統射出製程,體積收縮率在-2.9%~2.323%之間;
圖(b)為IMMC製程,體積收縮率在-3.7%~0.69%之間。
(a)
(b)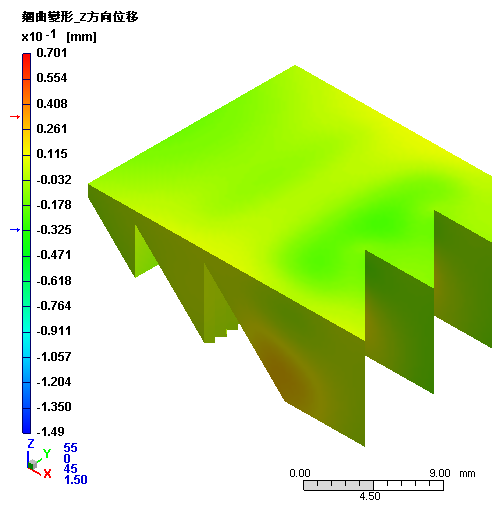
圖五 翹曲分析中的Z方向位移:圖(a)為傳統射出製程,Z方向位移範圍為-1.497~0.701mm;
圖(b)為IMMC製程,Z方向位移範圍為-0.325~0.311mm。
比較兩種製程的總和光彈條紋分析結果(圖六)則可發現,傳統製程在澆口處的光彈條紋變化劇烈,表示有較大的殘留應力,應是使用較大的保壓壓力所造成。而在IMMC製程中,因為有模內壓縮的輔助,可降低澆口壓力,所以澆口處的條紋變化較不劇烈。
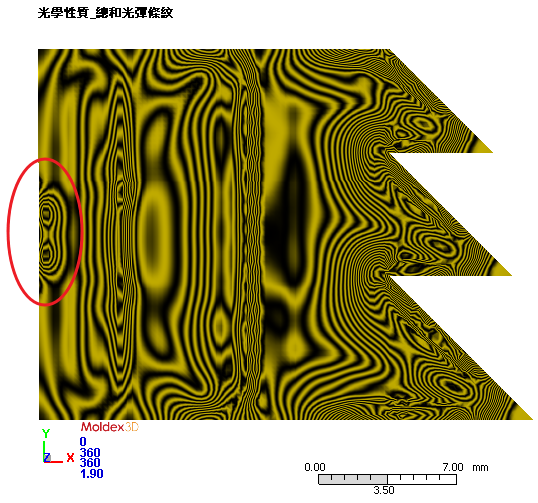
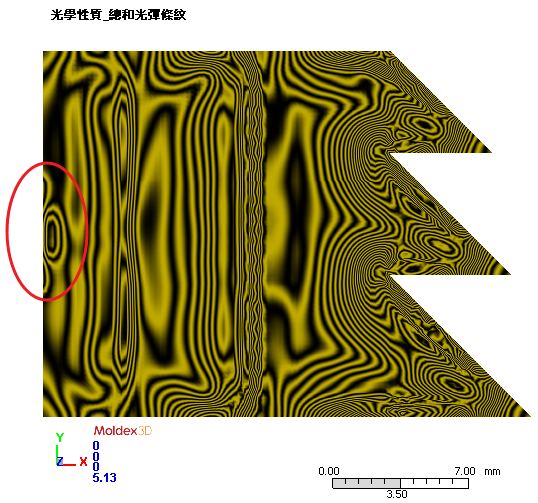
圖六 傳統射出成型製程(左圖)與IMMC製程(右圖)的總和光彈條紋分析比較
完成模流分析後,便進行實際試模,以驗證Moldex3D分析結果的準確度。Moldex3D的分析與實際驗證結果都顯示,在射出成型製程中,產品的兩狹縫會造成壓力傳遞困難,造成產品後端有凹痕產生(圖七)。改用模內階段式射壓成型(IMMC)製程後,可成功開發無凹痕的產品(圖八)。
圖七 Moldex3D凹痕模擬分析結果分析(圖左)與實際試模(圖右)結果高度一致
圖八 模內階段式射壓成型開發的產品無表面缺陷
結論
在產品的光照度部分,實驗室以LED燈泡照射方式進行驗證。經六次取樣,傳統製程與射壓製程的平均光照度分別為299Lux和321Lux,射壓製程的光照度獲得7.35%提升。最後使用光彈條紋量測機台進行光彈條紋的驗證。從圖九可發現,模流分析和實際實驗結果高度吻合,也證明Moldex3D對光彈條紋預測分析準確度十分精確。
由以上量測結果可證明,Moldex3D的分析與實際試模結果有高度一致性,有助於驗證新製程是否有助於開發複合式稜鏡。若缺少Moldex3D模擬輔助成型這個過程,會浪費不必要的設計與加工費用;萬一壓縮製程無法如預期提升導光效果,開發過程的損失將難以估計。