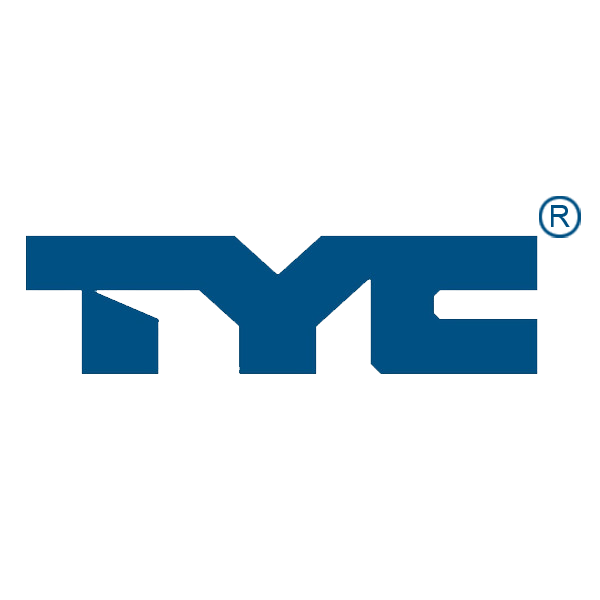
- 客戶: 堤維西交通工業股份有限公司
- 國家: Taiwan
- 產業: 汽車
- 解決方案: Moldex3D Advanced
大綱
第三煞車燈可以警示後方車輛,縮短發生緊急狀況時的煞車距離,減少發生逾50%的尾部追撞事故,使得第三煞車燈成為不可或缺的重要汽車配件之一。然而,第三煞車燈的設計偏向細長型,使得燈殼底座中央的開口過窄,形成散熱不均,容易發生變形,進而與其他構件發生組裝問題。堤維西透過Moldex3D塑膠模流分析解決方案,找出產品翹曲變形的原因,並藉由模擬分析,完成設計變更驗證,設計出成功改善良率的煞車燈件,省去高額的修模時間和成本。
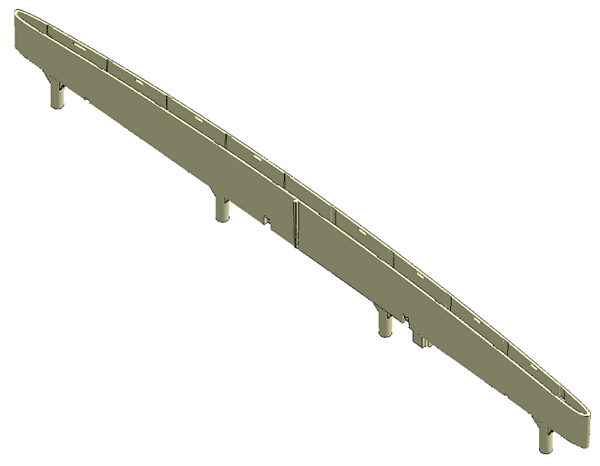
圖1 第三煞車燈 圖2 產品設計
挑戰
- 改善30%以上的產品變形
- 提高良品率
- 縮短組裝時間
效益
- 內縮改善率達57.4%。
- 良品率由62.7%提高至98.2%。
- 平均組裝工時由原本的434秒減至257秒。
案例研究
本案例中的產品,由於外形結構的緣故,產品可能會於成型過程中,發生內縮變形 (圖3 A處)。此內縮問題不僅會影響產品外觀,更可能導致燈殼在組裝時與底座無法接合(圖4),進而產生導光元件與LED電路板組裝困難以及其他製程上的問題。
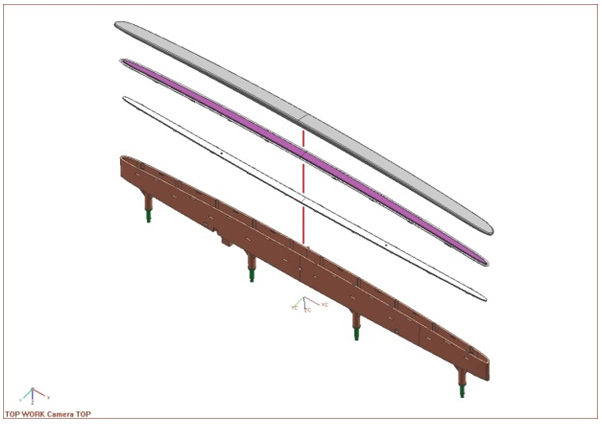
圖3 燈殼底座 圖4 第三煞車燈組裝順序
透過Moldex3D 塑膠射出模擬分析軟體,堤維西發現原始產品設計有模溫不均及產品中央內縮變形量過大等問題,且產品凹槽內部也有積熱情形,容易造成變形。為了使內縮尺寸控制在容許值內,堤維西利用Moldex3D進行兩種設計變更分析和驗證,希望提高散熱效果和減少翹曲變形。在維持原始設計的成形條件下,設計變更1 是修改水路並將入子的材料由P-5鋼材更換為鈹銅(圖5(b));設計變更2 則是在鋼材入子中設置直徑3mm的循環水路(如圖5(c)所示)。
由圖6(a)可知,原始設計之最大變形位置出現在產品兩端。設計變更1更換入子材料,改善了原始設計散熱不均的問題,也改善了Y方向的翹曲位移(圖6(b));而設計變更2 改良水路設計後,更能有效消除積熱,翹曲改善也更加顯著(圖6(c))。
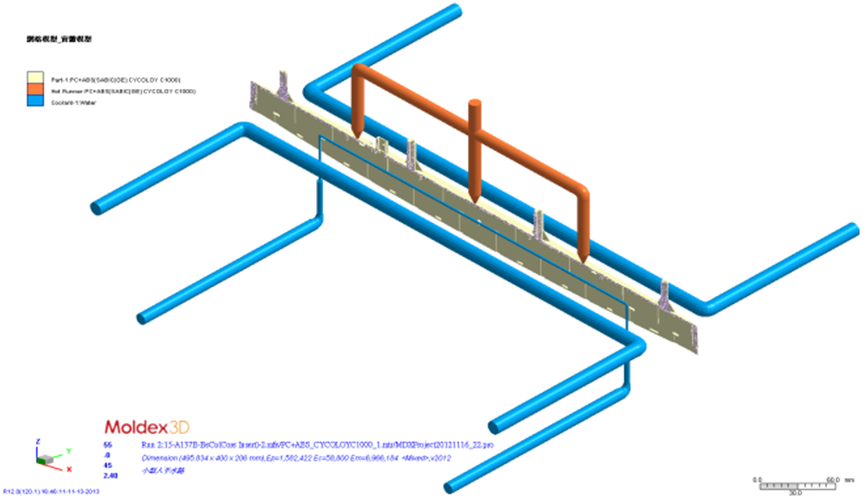
圖5 (a) 原始設計 圖5 (b) 設計變更1 圖5 (c) 設計變更2
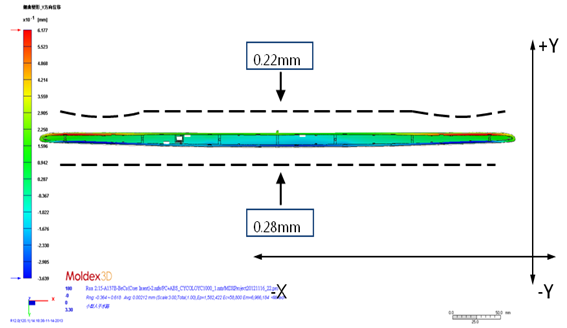
圖6 (a) 原始設計-翹曲分析 圖6 (b) 設計變更1-翹曲分析 圖6 (c) 設計變更2-翹曲分析
結果
經Moldex3D模擬分析和實務驗證後證實,設計變更2 的內縮改善幅度最大,最大改善率可達57.4%。此外,在生產良率和組裝工時的比較上(表2),設計變更2也是最佳的方案;良率提升至98.2%,平均組裝工時也從原本的434秒降低到257秒。透過Moldex3D卓越的分析能力,堤維西團隊能快速掌握產品設計問題,朝正確的方向進行設計變更。無須實際試模,透過Moldex3D即可進行各種設計變更比較,從中選出最優化設計,成功降低內縮變形量,大幅節省組裝人力與時間成本,讓Moldex3D成為未來產品開發的一大利器。
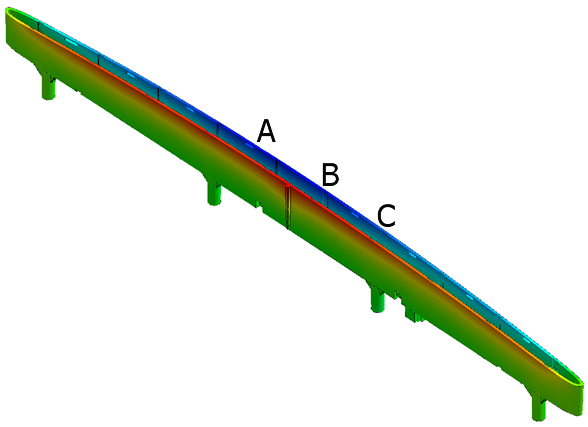
圖7 (a) 實際產品 圖7 (b) 分析結果
表1 實際產品(左)與模擬分析(右)變形量比對
原始設計 | 設計變更1 | 設計變更2 | |
生產數量 | 1000pcs | 1000pcs | 1000pcs |
組裝後良品數 | 627pcs | 836pcs | 982pcs |
良品率 | 62.7% | 83.6% | 98.2% |
平均組裝工時 | 434sec | 366sec | 257sec |