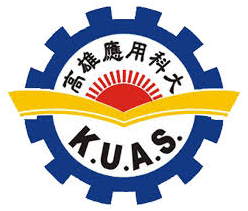
- 客戶: 高雄應用科技大學
- 地區:台灣
- 產業: 教育
- 解決方案:Moldex3D Advanced;MCM
(來源: www.kuas.edu.tw)
大綱
塑膠厚件產品的射出成型問題層出不窮,表面凹陷、噴流痕、真空泡等都是常見的瑕疵。此外由於厚件的溫度傳遞效果差,而需要較長的冷卻時間,嚴重影響生產效率。本案例研究一厚度達12mm的塑膠光學鏡片產品,利用分層多次射出的概念將成品以B-A-B的形式進行射出成型,藉由Moldex3D多材質射出成型(MCM)模組來分析A 層與B層的厚度改變對冷卻時間及光學性質的影響,期望能藉此找到最佳的各層厚度組合,達到高品質光學產品並縮短製造週期。
挑戰
- 找到最佳的厚度組合,以縮短冷卻時間
- 透明度、殘留應力等光學條件都達到較佳的結果
解決方案
使用Moldex3D 多材質射出成型(MCM)模組設計產品最適當的各層厚度,期望縮短冷卻時間
效益
- 冷卻時間成功縮短50-60%
- 凹陷量減少了85%
- 設計變更後消除了大部分的殘留應力,並與Moldex3D預測結果符合
案例研究
本案例產品為厚度達12mm的光學鏡片產品(圖一),希望藉由分層多次射出製程,調整該產品的各層厚度比例,以達到較佳的光學品質並縮短冷卻時間。原始設計面臨了冷卻時間過長的問題,根據Moldex3D的模擬,要將產品冷卻到頂出溫度,整整需要384秒。此外Moldex3D翹曲分析中也偵測到嚴重的凹痕,是厚件散熱不佳所導致。
圖一 本案例的12mm厚件光學鏡片
為解決此問題,高應大團隊導入了多材質射出成型製程。第一射產生厚件的中間層(A層),第二射則產生上下兩層(B層),以完成此厚件產品(圖二)。接下來要面對的問題是:每一射所產出的厚度應如何定義?高應大團隊於是提出了4項設計變更,並透過Moldex3D一一模擬驗證,以觀察不同厚度組合的冷卻時間差異。根據Moldex3D冷卻分析結果,中間層6mm和上下兩層各3mm的產品設計,可以達到最短的冷卻時間─172秒,比原本的冷卻時間縮短了55%(圖三)。
圖二 產品的中間和上下層是由兩次射出產生
圖三 設計修改後,冷卻時間由384秒降為172秒
原始設計的殘留應力量測結果,與Moldex3D光彈條紋分析結果一致(圖四)。接下來進行產品的凹痕及透明度等光學性質的檢驗,檢驗結果(圖五)顯示,凹陷量有顯著的改善,並隨著產品上下層的厚度呈等比例變化。而設變的透明度也與原始設計不相上下。
圖四 原始設計的殘留應力量測與Moldex3D光彈條紋分析趨勢相符
圖五 凹陷量及透明度量測結果
結果
Moldex3D預測厚件光學產品冷卻時間和相關光學性質的能力,對於改善光學鏡片設計品質有很大的助益。從殘留應力量測的結果也可發現Moldex3D模擬結果是可靠且貼近真實的。高應大藉由Moldex3D找到優化的產品分層厚度組合、縮短了高達55%的冷卻時間,也獲得良好的光學品質。