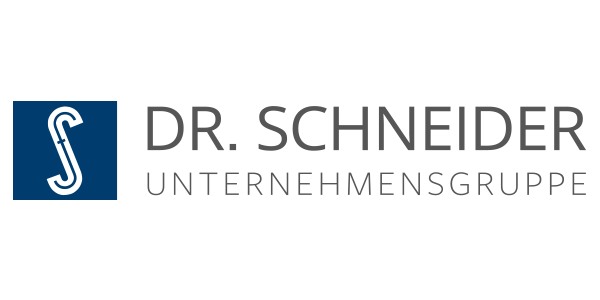
- 客戶:Dr. Schneider
- 國家:波蘭
- 產業:汽車
- 解決方案:Moldex3D Advanced; Flow、 Pack、 Cool、Warp、MCM、Digimat-RP、Fiber、FEA Interface、Expert、Advanced Hot Runner、Viscoelasticity、CADdoctor
大綱
施耐德博士集團CAE工程師Przemyslaw Narowski分享了公司為何選擇Moldex3D,作為改善射出成型問題的模擬工具。他們運用Moldex3D驗證新產品設計的可行性研究,並擴展其技術力至未來的應用,更讓CAD、CAE到CAM流程的串聯更加順暢。本文以多項實際案例呈現Moldex3D模擬的準確性以及為產業帶來的價值。
挑戰
- 產品包封問題
- 產品嚴重翹曲變形,影響裝配
- 須縮短產品研發時間
解決方案
濾油器案例中,Moldex3D幫助改善了40%的翹曲問題,使產品符合所需的規格;汽車内飾件案例中,Moldex3D則協助解決了包封問題,避免外觀缺陷。
效益
- 成功驗證Moldex3D模擬與實驗結果的一致性
- 翹曲問題改善40%
- 找到合適的排氣位置來預防包封問題
- 啟發了「逆向模擬」的概念,可以做為未來產品開發的方向
案例研究
本文案例中,目的為驗證Moldex3D模擬與實驗結果的一致性,再進一步用於產品翹曲的改善與解決包封問題。
在第一個案例,施耐德博士集團以Moldex3D模擬一汽車主要元件的翹曲行為(圖一)以及車內收納盒的控制桿 (圖二),結果顯示模擬與實驗結果相符。
圖一 汽車導引元件翹曲模擬結果與實際試模比較
圖二 控制桿翹曲模擬結果與實際試模比較
第二個案例中,濾油器元件的控制桿和蓋子的新設計,經Moldex3D偵測出有潛在的嚴重翹曲和包封問題。兩者都會造成裝配困難,並影響產品外觀。
為改善上述問題,施耐德博士集團提出新的產品設計方案,並透過Moldex3D的幫助,在產品收縮最嚴重的區域減少一半的料(圖三),並在Moldex3D預測出的區域設計了合適的排氣位置(圖四)。變更後的設計由於產品厚度縮小,Moldex3D的模擬結果顯示翹曲情形已獲得有效改善。
圖三 在新的產品設計中,將收縮最高的部位減料一半
圖四 Moldex3D可準確預測包封位置,並用來設置合適的排氣位置
設計變更之後,再以Moldex3D模擬原始設計和優化設計。原始設計的翹曲分析結果顯示出,產品肉厚處會有較高的收縮率,導致翹曲量過大(圖五)。而由於肉厚改變的設計變更,翹曲量大幅縮減了40%(圖六)。
圖五 原始設計的翹曲量過大
圖六 設計變更後,翹曲量減少了將近40%
結果
有了Moldex3D的幫助,施耐德博士集團得以了解模內充填和翹曲行為,在實際生產前就可以預測出可能的缺陷問題。對他們來說,Moldex3D已是新產品設計可行性研究中,不可或缺的工具。所有在CAD系統中繪製的產品幾何,都會先經由CAE分析後,才進行射出成型製造。若發現哪裡出了問題,尤其是翹曲量超過可接受範圍時,就會採取適當的對應措施。施耐德博士集團最後也成功解決了製造難題、優化產品和模具設計,有效降低試模和修模成本。